Latest News
May 1, 2011
By Vince Adams
SIMULIA, the Dassault Systèmes brand for simulation based out of Providence, RI, wants to democratize multiphysics, or MP. This is an exciting direction from the makers of Abaqus, considered by many to be the high-end of high-end finite element analysis (FEA) products.
![]() The Feature Tree and toolbar layout in Abaqus/ CAE adapts automatically to the multiphysics domain active in a current session. |
Eric Weybrant, SIMULIA’s product manager for analysis products, says the company’s vision is to make simulation an integral business practice for product development organizations. This means fewer assumptions with more realistic analyses. Accessible MP is the key to making this happen. Abaqus, with its standard (implicit) and explicit solvers, has always had components of MP—and with Abaqus 6.10, released last summer, and 6.11 scheduled to be released this month, the developer says the end goal is in sight.
MP 101
Over the past decade, the definition of MP simulation has evolved to encompass the incorporation of two or more traditionally isolated analytical domains into a solution that reflects the combined results of each. These analytical domains might include stress/deformation, thermal, computational fluid dynamics (CFD), electromagnetics (EM), acoustics and—in the eyes of some—multi-body dynamics (MBD).
![]() Abaqus/CFD analysis of transient thermal analysis of an engine exhaust system. |
SIMULIA expands this definition to include simulation across greatly different scales, such as molecular and macros sizes.
Fluid-structure interaction (FSI), or the coupling of fluid flow fields with deformable or moving solids with bi-directional feedback, was the breakthrough that brought the term multiphysics into the common product development engineer’s world.
MP requires that the inputs and outputs of the various domains be coupled. This is handled in a few different ways. When physical responses are one-directional—such as negligible deformation of a stiff solid in a flow stream—direct sequential, often manual, coupling of the results is sufficient. The pressure field from a CFD solve is applied to the solid structure, and stress is computed.
FSI, as implemented in Abaqus 6.10, provides a simultaneous solution of multiple domains, where the results of many staggered solutions are used to obtain bi-directional equilibrium. Thus, the true or natural response of the system to the various physics applied can be determined.
Finally, MP models can be coupled within a single mesh or across distinct domains. Coupled thermal flow with thermal stress effects on a solid mesh represents one application of a single mesh solution.
Multi-domain models are the most difficult computationally, but are also the most versatile. These are typically discontinuous at the domain boundaries—and constantly changing, requiring sophisticated management of the interactions. However, each mesh can be optimized for that particular domain (CFD vs. stress, for example), for more efficient solutions.
Coupled Euler-Lagrangian Model
Abaqus 6.10 supports multi-domain models using a coupled Euler-Lagrangian (CEL) method. This is an important concept in FSI, but requires some explanation for non-CFD specialists.
At the risk of over-simplifying, an Eulerian model is common in CFD, where the field variable changes within a fixed mesh. A Lagrangian model is characterized by a deformable mesh. The boundaries change as the solution progresses. This is typical of structural FEA problems.
Efficient modeling of FSI with deformable bodies requires the best of both worlds. CEL provides for the creation of an Eulerian fluid mesh within a Lagrangian solid body. Abaqus couples these models by enforcing the boundary of the fluid domain to map to and stay “attached” to the deforming solid mesh. The computation of sloshing in a deformable tank is made possible by this technique.
Abaqus/CFD for HPC
The CFD capabilities in Abaqus/CFD, new in Abaqus 6.10, were written from scratch by SIMULIA with high performance computing (HPC) in mind. While more difficult than incorporating an existing CFD solver, ground-up development provides potential for leveraging massively parallel solving technology that might not have been anticipated 10 years ago. Large problems are common in the MP world, and model sizes will continue to grow.
In addition to the CEL algorithm, Abaqus/CFD has also integrated smoothed-particle hydrodynamics (SPH), which uses mathematically generated points within a fixed mesh to represent the movement of the fluid. This technology is well suited to complex flow boundary problems, and expands the size of the problem set that can be addressed in Abaqus multiphysics.
Abaqus/CFD currently only solves incompressible flow problems, but does incorporate transient and turbulent conditions. This is sufficient for many common FSI or MP problems.
Abaqus/CAE pre- and post-processing for CFD was released simultaneously, with all the visualization capabilities experienced CFD users have come to expect. This includes multiple section views, and streamlined calculation.
MP in Abaqus 6.10
SIMULIA has grown its MP capabilities by working closely with customers and responding to their needs, Weybrant says. With the incorporation of CFD in Version 6.10, and EM in Version 6.11, Abaqus will have all the building blocks to tackle commonly understood MP challenges, he adds.
In a SIMULIA press release, Dr. Fred Yang, technical leader of bearing analysis from Federal-Mogul Powertrain Sealing and Bearings Group USA, says his company is pleased that Abaqus provides the CFD capabilities for FSI, which enables his team “to perform accurate fluid and solid co-simulations.
“The new solution certainly gives us significant enhancements to explore multiphysics interaction in our designs, and optimize our products to reduce engine power loss and lower overall material costs,” he adds.
While FSI and HPC are native to the product, an important focus of the development team is to identify existing problems of commercial and social importance, such as hybrid electric vehicle (HEV) design, and expand the MP capabilities available to these challenges. Vertical, industry-specific products are planned to address these growing needs. This will require expanding the boundaries of the simulation workspace.
One example of expanded boundaries is the ability to integrate Dymola models, from the CATIA division of parent corporation Dassault Systèmes, into 3D MP problems. Dymola is a 1D system-modeling tool that can capture logic statements, external energy flows and control algorithms.
SIMULIA is working on the infrastructure to ensure support for real-world MP problems—even considering MP possibilities that aren’t yet commercially available. Understanding that the right technology might come from other research organizations, SIMULIA has provided a unified framework for all MP tools with a network of more than 100 partners offering complementary technology.
MP for Product Development
MP coupling can be intimidating for design engineers who are primarily trained to model stress/deformation problems. SIMULIA is working to build this additional functionality into the current workflows with which a structural engineer would be comfortable.
To start with, Abaqus/CAE, the pre- and post-processing environment popular among Abaqus users, is the chosen platform for MP modeling. Users create a separate “model” in the feature tree for each domain. All common modeling tasks, such as meshing, selection and manipulation, are consistent by definition. Domain-specific needs, such as boundary condition and material definition, are incorporated using familiar forms and formats so that a structural user can focus on the engineering application—and not have to learn a new workflow.
Once the models of each physical domain are complete, Abaqus/CAE allows for co-execution of the system. This initiates the MP solution. A separate solver job is created for each model, but the coupling is done automatically.
In fact, SIMULIA has built most of the coupling into the background, thus eliminating repetitive definitions or redundant tasks. Abaqus 6.10 has also implemented “High Level Application Parameters” that set solver defaults to the most commonly used and effective values behind the scenes, based on user research, to make it easier for engineers to explore new or infrequent modeling combinations.
Once complete, the results of each job can be viewed independently in Abaqus/CAE or overlaid upon each other for a complete snapshot of the system response.
“Using FEA provides us with a more sophisticated method to understand and predict realistic behavior of complex geological environments,” Phil McCurdy, principal geomechanics engineer for Senergy, said in a SIMULA press release. “We selected Abaqus due to its industry-proven track record and well documented use cases. Its open architecture also gives us the potential to link reservoir geomechanics models and flow models for more precise co-simulation and multiphysics solutions.”
All Dassault Systèmes brands are starting to integrate MP with user-level appropriate products, including expert- and designer-focused products. The impact of this can already be seen in the latest releases of the integrated simulation tools in SolidWorks and Catia.
Weybrant is quick to point out that this is not a simplification of MP technology, but a repackaging to make advanced technologies more accessible: “Multiphysics must be accessible if it is going to be integrated into the engineering of real-world products.”
More Info:
Dassault Systèmes
Federal-Mogul Powertrain
Sealing and Bearings Group USA
Senergy
Vince Adams, currently an account manager for LMS, is a longtime simulation educator, consultant and speaker. He has authored three books on finite element analysis and numerous magazine articles.
Subscribe to our FREE magazine,
FREE email newsletters or both!Latest News
About the Author

DE’s editors contribute news and new product announcements to Digital Engineering.
Press releases may be sent to them via [email protected].
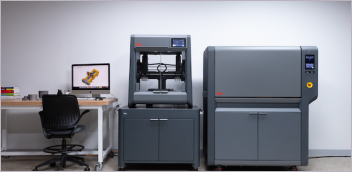
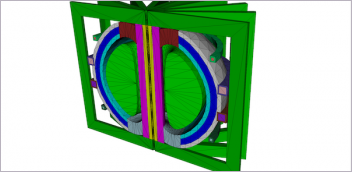
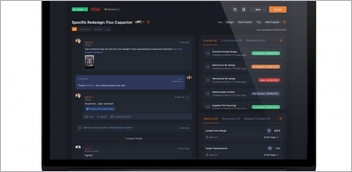
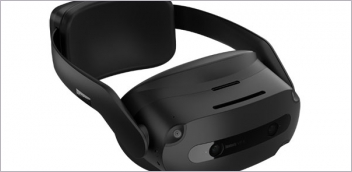