Latest News
January 17, 2011
By DE Editors
![]() |
Safe Technology Ltd. (Sheffield UK and Dearborn, MI), developers of the fe-safe durability analysis software for finite element models, has launched fe-safe/Composites, a new product for the analysis of fatigue in composite materials. According to the company, fe-safe/Composites extends the capabilities of the company’s fe-safe durability analysis software to include the analysis of composite materials, enabling engineers to calculate complex loading histories that previously have only been available for use with metals.
Developed in collaboration with Firehole Technologies (Laramie, WY), fe-safe/Composites leverages Firehole’s Helius:Fatigue technology to enable its fatigue analysis of composite materials. Helius:Fatigue combines the constituent-based failure analysis method called Multicontinuum Theory (MCT) with the kinetic theory of fracture to enable fatigue life prediction in composite structures. Helius:Fatigue does not require “exotic material data” nor does it required “substantial computational cost,” according to the companies. Helius Material Manager comes with a “comprehensive” database of materials properties, and you can extend and modify the material properties.
fe-safe/Composites is described as a robust and computationally efficient tool for predicting fatigue life in composite structures comprising unidirectional laminae. It can be used to predict lamina-level fatigue life at every integration point in an FE (finite element) model as well as predict fatigue failure by its ability to apply kinetic theory to constituent-level stresses, according to the company. The software is said to apply “realistic” physics to “naturally account for the effects of frequency, mean stress, and combined loading.
![]() |
With fe-safe/Composites, users reportedly can simulate real-world industrial loading conditions. Citing the ability of fe-safe to use different fatigue algorithms for different sections of an FE model, Safe Technology says that users can also combine the analysis of composites and the analysis of metals in the same run. Capabilities for calculated cycles to failure available in fe-safe/Composites include:
- Calculated for each individual cycle
- Calculated using the kinetic theory of fracture to determine failure in the matrix constituent
- Predicted for two failure modes: Matrix damage parallel to fibers (transverse) and matrix damage perpendicular to fibers that leads to fiber failure (longitudinal)
![]() |
fe-safe/Composites allows to mix the analysis of solid and shell elements in the same model, and, says the company, there is “no effective in-built limit to the number of elements in the model or the file size.” Input capabilities include standard material properties for the composite lamina and elastic constants. These and other load conditions can be combined and superimposed with great flexibility, says the company. The software requires only standard, static material properties and minimal fatigue characterization, an fe-safe/Composites can handle arbitrarily complex load histories.
Safe Technology reports that e-safe/Composites includes capabilities for PSDs, dynamics, rainflow matrices, and others. Supported file formats for component loading include .DAC, single and multi-channel ASCII, Safe Technology .amc, RPCIII, Servotest, Snap-master, as well as others. All file formats are read directly without file converters, notes the company.
“Our companies make a formidable partnership, each the technical leader in our specialist field; Firehole in advanced composites analysis and Safe Technology in durability analysis from FEA,” said John Draper, CEO, Safe Technology Ltd., in a statement released to the press. “Our teams have worked well together during the development of ]fe-safe/Composites], and we are confident that we can meet the rigorous demands the composites industry will make on this technology.”
![]() |
fe-safe/Composites comes with interfaces such widely deployed FEA solutions as Abaqus, Altair HyperMesh, ANSYS, and Pro/Mechanica as well as versions of Nastran from MSC.Software, Noran Engineering, and Siemens PLM Software. fe-safe/Composites, which currently supports Windows only whereas fe-safe supports Windows, Linux, and UNIX, is available from Safe Technology directly or through its reseller network. For more information, visit Safe Technology Ltd.
Read an overview of the capabilities available in fe-safe/Composites.
Register for an introductory webinar on the features and functionality of fe-safe/Composites.
Learn about training courses and seminars offered by Safe Technology.
Download the fe-safe/Composites brochure.
Go here for more details on Helius:Fatigue.
See why DE’s Editor’s selected fe-safe/Composites as their Pick of the Week.
Sources: Press materials received from the company and additional information gleaned from the company’s website.
Subscribe to our FREE magazine,
FREE email newsletters or both!Latest News
About the Author

DE’s editors contribute news and new product announcements to Digital Engineering.
Press releases may be sent to them via [email protected].
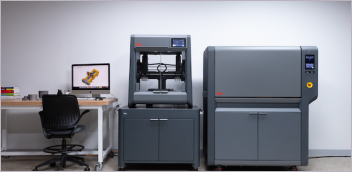
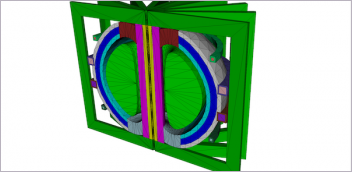
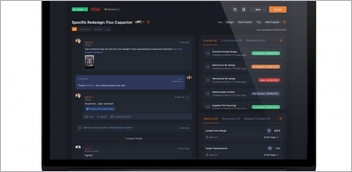
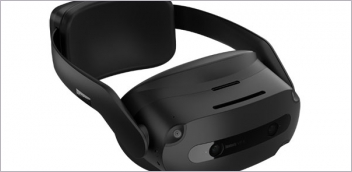