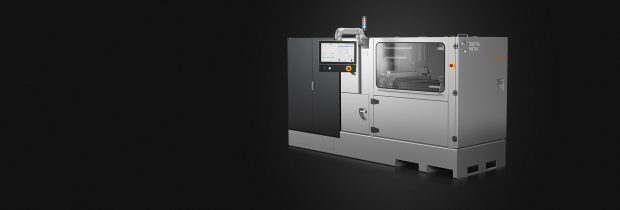
The DM P2500 uses Digital Metal’s proprietary binder jetting technology to 3D print high-accuracy metal parts. Image courtesy of Digital Metal.
Latest News
October 25, 2017
Digital Metal offers commercial availability of its DM P2500, a high-precision binder jetting 3D metal printer that can produce small and intricate components. The company reports that, as part of its production service, it used its proprietary binder jetting technology for four years to fabricate approximately 200,000 pieces for customers in several industries, including aerospace, luxury goods, dental tools and industrial equipment manufacturing.

The company describes the DM P2500 as made for serial production and customized parts. It can continuously print in 42 µm layers at 100 cc/hr. (6.1 cubic in./hr.) without requiring support structures. It has a 203x180x69-mm (LxWxH; 8x7x2.7-in.) build area.
Digital Metal says that with the DM P2500 users can manufacture small objects in high quantities—up to 50,000 parts in one print run—adding that the system can 3D print objects with various shapes, geometries and internal and external finishes. The DM P2500 delivers a resolution of 35 µm and an average profile surface roughness parameter of Ra 6 µm before additional finishing processes.

The DM P2500 can 3D print complex architectures with medical grade smoothness on a small scale, and it can make components with moving parts within other objects as well as a gradient of holes in a single print, the company says. Digital Metal explains that the DM P2500's process is adaptable for various materials because the heat treatment (sintering) occurs after printing. Powder removed before sintering can be reused for subsequent jobs. This results in high yield and low scrap rates and it minimizes downtime, according to the company.

Materials for the DM P2500 include stainless steel 316L (1.4404), stainless steel 17-4PH (1.4542) and Ti-6Al-4V titanium. Miscellaneous operational characteristics include 15- to 25-minute changeovers between print jobs, room temperature operation, no need for protective atmosphere or inert gases, and automatic calibration of the build box. The system's software enables high detail accuracy and traceability of process parameters, adds Digital Metal.

In a complementary statement in the U.S., Digital Metal reports that it and Honeywell Aerospace are exploring a number of joint 3D printing projects that will merge Honeywell’s expertise in aerospace engineering with Digital Metal’s binder jetting 3D metal additive manufacturing capability.
“The binder jetting technology Digital Metal uses to print small metal parts has the potential for various applications within the Honeywell Aerospace program,” said Don Godfrey, engineering fellow—Additive Manufacturing, Honeywell Aerospace in a testimonial supplied by Digital Metal. “We believe this will also be critical to applications in other key areas of the broader aerospace industry.”
Digital Metal also provides optional ancillary equipment for the DM P2500 including a downdraft table for powder handling and a cleaning cabinet for powder separation from components after 3D printing. Introductory and ongoing training and support are also offered.

Digital Metal is a company within the Höganäs Group, a producer of iron and non-ferrous metal powders headquartered in Höganäs, Sweden, and with 13 offices worldwide. The DM P2500 can be purchased or licensed from Digital Metal.
For more information on the DM P2500, click here.
Watch an introduction to Digital Metal and its 3D print technology.
Read how the Digital Metal binder jetting process works.
Download the DM P2500 brochure.
Watch how Montfort Watches uses the DM P2500.
Read some use cases.
See why DE's Editors selected the DM P2500 as their Pick of the Week.
Sources: Press materials received from the company and additional information gleaned from the company's website.
Subscribe to our FREE magazine,
FREE email newsletters or both!Latest News
About the Author

Anthony J. Lockwood is Digital Engineering’s founding editor. He is now retired. Contact him via [email protected].
Follow DE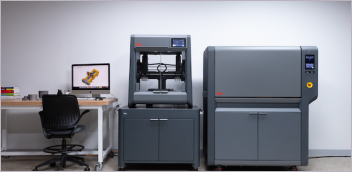
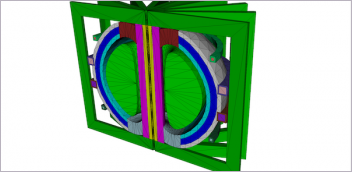
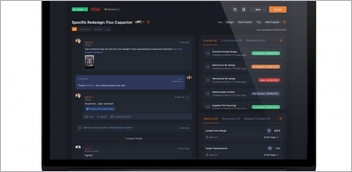
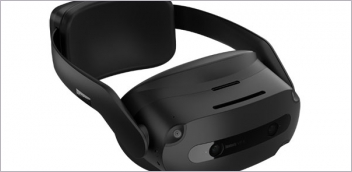