Blind Man `Sees’ New Home through Model
3D Systems' SLAr and SLSr processes featured on ABC's "Extreme Makeover: Home Edition."
Latest News
May 1, 2008
By 3D Systems
![]() The Hughes family celebrates their new home with a DuraForm® PA Plasticmodel on ABC’s “Extreme Makeover: Home Edition.” Courtesy of Pfoto.com |
The benefits of the Direct Manufacturing of plastic models — with 3D Systems’ technology — hit prime-time television.
The University of Louisville’s Rapid Prototyping Center (Louisville, KY) and Harvest Technologies (parts service provider; Belton, TX), teamed up to build SLA® and SLS® models of a home for a family featured on ABC’s “Extreme Makeover: Home Edition.”
The “Extreme Makeover” team rebuilt in just seven days the Hughes family home in Louisville, KY, to be safe and wheelchair accessible for the eldest son, Patrick Henry, a blind and disabled college student who has overcome challenges to become a musician and an inspiration. The show aired on ABC in late February.
![]() A CAD file of the model of the new, improved Hughes family home.Courtesy of UL Rapid Prototyping Center |
Patrick Henry was given the Dura-Form® PA and Accura® 25 models, two ‘Go Pro’ materials from 3D Systems (Rock Hill, SC), so he could “see” the shape and layout through touch at the same time the crowd chanted “move that bus” and his family was experiencing the surprise of visually seeing their new, improved home.
“He would have had no idea what the house looked like or understand the floor plan to get around without our models,” said Tim Gornet of the University’s RPC at the J.B. Speed School of Engineering.
With a 48-hour deadline, contractor Elite Homes asked the university to build a model. The university’s RPC created in a day a three-dimensional CAD drawing from two-dimensional design layouts of the home.
![]() The university and Harvest used this CAD file to build the layout of the home.Courtesy of UL Rapid Prototyping Center |
The RPC successfully built a nine-piece, scaled-down plastic model on a 3D Systems’ SLS® System with DuraForm® PA Plastic, a durable and functional nylon material that has excellent surface resolution. It took 22 hours to build the 18 by 15 by 7-inch model.
Meanwhile Harvest, a partner to the university for this project, built a slightly larger three-piece model of the home. The roof and ceiling were made with Accura® 25 Plastic, a flexible material that simulates the aesthetics and properties of polypropylene, on a 3D Systems’ accurate, reliable Viper Pro SLA® System. A Sinterstation® Pro SLS® System, known for its high throughput and speed, created the body of the house — built in Dura-Form® PA Plastic.
The models were completed late Tuesday, delivered to the contractors early Wednesday and presented to Patrick Henry later that day.
“The models were exactly what we expected and more,” said Joe Pusateri, president of the Elite Homes. “The roof was removable so Patrick could put his hands in the house and feel where the walls were located. He lived in a non-handicapped accessible home where he learned his way around. He was going to have to learn a new route in the new home.
The RPC model now sits in Patrick Henry’s bedroom, while Elite Homes is displaying the Harvest model with plans to paint it to look like a miniature version of the house as a memento of that special week.
Information:
3D Systems
Rock Hill, SC
803-326-4080
3dsystems.com
Subscribe to our FREE magazine,
FREE email newsletters or both!Latest News
About the Author

DE’s editors contribute news and new product announcements to Digital Engineering.
Press releases may be sent to them via [email protected].
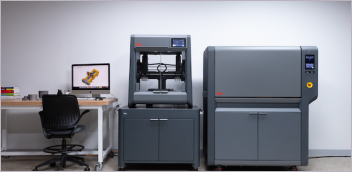
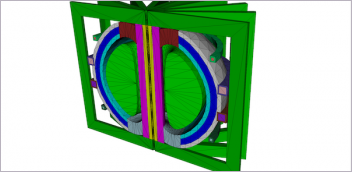
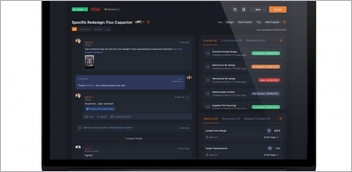
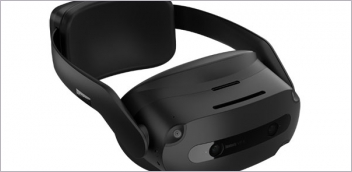