Cideon Engineering GmbH Relies on Femap and NX Nastran for Railway Vehicle Design
World-renowned design company uses computer simulation with Femap and NX Nastran for safer, more efficient railway vehicle design.
Latest News
June 17, 2008
By DE Editors
With a customer portfolio that includes world class railway vehicle manufacturers Siemens, Vossloh, Bombardier, Alstom, Stadler and Deutsche Bahn, Cideon Engineering GmbH develops anything that runs on rails including high-performance locomotives, switchers, mining locomotives and railway construction vehicles, as well as railway cars and street cars.
The company also provides customers with services such as project planning, business consulting, mechanical design engineering, trial monitoring, construction supervision, approval procedures and professional assessments.
Founded in 1992 under the name IKB as a provider of engineering services Cideon Engineering GmbH started out as a 10-man company and has grown its manpower to more than 100 employees with two offices in Germany. In 2002, the company changed its name to Cideon Engineering GmbH, which together with the companies Cideon Systems and Cideon Software, belongs to Cideon AG, a corporate group with a headcount of approximately 170.
![]() ![]() ![]() ![]() |
Besides railway vehicles, Cideon Engineering GmbH also develops production equipment for the automotive industry. More than 80 percent of the company’s activity involves railway vehicles.
Computer simulation is critical during the design process and Cideon Engineering uses tools such as the NX Nastran finite element analysis (FEA) solver and the Femap pre- and post-processor. Femap was selected because it has a very solid cost-performance ratio, excellent integration with leading CAD systems and options for visualizing the analysis results.
In railway vehicle design, each part is analyzed separately due to the fact that there are specific rules relating to the performance of each individual part. Engineers perform linear static analyses but occasionally also vibration analysis and the examination of contact problems.
An analysis project begins with importing the CAD data, which is then simplified and cleaned up, then converted to a surface or finite element shell model so that the analysis calculations can be performed more quickly. Some of the meshing can be done using Femap’s automatic meshing tools while other parts of the mesh are created manually. Models consist of 120,000 or more elements, depending on the design and parts involved. The solving of an analysis of such a model using the NX Nastran solver on an up-to-date Windows PC takes approximately two minutes.
Once an analysis has been completed successfully, the specialists at Cideon Engineering use Femap to visualize and evaluate the results. Femap includes a wide variety of tools for displaying displacements, tensions, forces as tables, diagrams and figures. Since Femap is a native Windows application, results can easily be transferred to other Windows applications such as Excel and Word.
For more information visit Siemens PLM Software.
Subscribe to our FREE magazine,
FREE email newsletters or both!Latest News
About the Author

DE’s editors contribute news and new product announcements to Digital Engineering.
Press releases may be sent to them via [email protected].
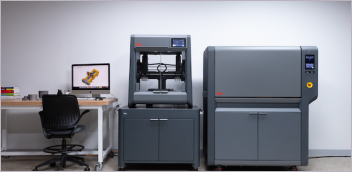
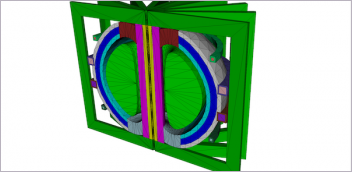
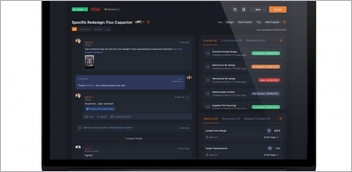
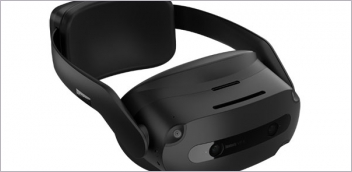