Latest News
May 18, 2012
By DE Editors
Highlights of COMSOL
|
COMSOL has announced the 4.3 release of COMSOL Multiphysics, its software environment for modeling and simulating any physics-based system. COMSOL Multiphysics 4.3 is designed to empower engineers, researchers and scientists with new modeling tools and fast simulations for electrical, mechanical, fluid flow and chemical applications. New capabilities introduced in version 4.3 include three new discipline-specific add-on modules, new meshing capabilities, a “Double Dogleg” solver for mechanical contact and highly nonlinear simulations, and numerous user-inspired enhancements.
Enhancements and upgraded functionality span the entire COMSOL product suite. With the debut of three new discipline-specific add-on modules—the Nonlinear Structural Materials Module, the Pipe Flow Module, and the Corrosion Module—COMSOL now offers 30 products for the simulation of multiphysics phenomena. The newest modules expand the COMSOL Multiphysics simulation platform with new user interfaces designed to help users solve the design challenges in each of these areas.
This geometric representation of a lung was
imported using the COMSOL CAD Import Module. The meshing algorithm creates a default mesh in 30
seconds on a standard dual-core workstation, according to COMSOL. Generating a coarser mesh takes10 seconds, when Virtual Geometry operations
are applied to minimize theinfluence of non-essential geometry edges and surfaces.
Geometry courtesy of Prof. Thomas Royston and Ying Peng, Acoustics & Vibrations Laboratory, University of Illinois at Chicago.
User-inspired Developments
“Our mission is to bring engineers and scientists reliable simulation tools that impact their day-to-day work, so their input is a crucial component of our product,” said Bjorn Sjodin, vice president of Product Management for COMSOL. “We’re continually soliciting and receiving feedback from our user base, while pursuing that passion for innovation that COMSOL is known for.”
COMSOL says many of the requested enhancements further increase the integration of COMSOL Multiphysics with the larger CAE community. For example, core modeling capabilities in version 4.3 have been updated and expanded significantly. Meshing is now both faster and more powerful, particularly when working with virtual geometry operations for shielding the automatic mesher from unnecessary geometric detail. Users working with imported meshes can now group existing mesh elements into new domains and boundaries, which makes it easy to assign boundary conditions and material properties wherever desired.
This geometric representation of a lung was imported using the COMSOL CAD
Import Module. The meshing algorithm creates a default mesh in 30 seconds on
a standard dual core workstation. Generating a coarser mesh takes 10 seconds,
when Virtual Geometry operations are applied to minimize the influence of
non-essential geometry edges and surfaces. Geometry courtesy of Prof. Thomas
Royston and Ying Peng, Acoustics & Vibrations Laboratory, University of Illinois
at Chicago.
Users can now run multiple-parameter sweeps by specifying one, two, or more parameters—sweeping for all of them or just a subset of them. Visualizations of results from these parameter sweeps can be selected to include combinations of the swept parameters in the one presentation. New Cluster Sweep and Batch Sweep user interfaces facilitate defining massively parallel and independent parametric sweeps.
Version 4.3’s modules for electrical, mechanical, fluid flow, and chemical
simulations have all been updated with new features and capabilities. COMSOL
implemented a user interface within the AC/DC Module for modeling 3D rotating
machinery.
The AC/DC Module now includes the ability to model rotating machinery in 3D. Here, a brushed DC motor simulated with the new 3D rotating machinery user interface is shown. Visualized are B-field, coil current, axial torque, and rotational angle.
Users of the Structural Mechanics and MEMS Modules can use a new solver for mechanical contact and highly nonlinear simulations—the “Double Dogleg” solver. New tools for tagging load cases have also been included for easier setup of extensive structural mechanics studies. The CFD Module introduces new interfaces and added functionality for mass transport simulations influenced by turbulent mixing, while the Particle Tracing Module now incorporates particle-particle interaction and Brownian forces into its extensive list of supported functionalities.
In this benchmark, a circular bar is subjected to a uniaxial tensile test, resulting
in large deformations. The bar experiences large-scale necking and plastic
deformation across its central cross-sectional region. This simulation is made
possible by the large strain plasticity option available in the Nonlinear Structural
Materials Module and the new, Double Dogleg solver.
Nonlinear Structural Materials Module
The new Nonlinear Structural Materials Module augments the mechanical capabilities of the Structural Mechanics and MEMS Modules by adding nonlinear material models. When the mechanical stress in a structure becomes large, certain nonlinearities in the material properties force the user to abandon linear material models. This situation also occurs in some operating conditions, such as high temperature. The new module adds elastoplastic, viscoplastic, creep, and hyperelastic material models. These are based on a new, extended framework for the constitutive laws, which COMSOL says users can easily extend for their unique needs.
Pipe Flow Module
The new Pipe Flow Module should interest engineers who design and optimize the pipe and channel networks used in turbines, building ventilation systems, chemical and material manufacture processes, and in the oil and gas industry. The module enables efficient simulations of 1D fluid flow, heat and mass transfer, hydraulic transients, and acoustics. The Pipe Flow Module’s simulation results can be integrated into 2D and 3D models of network components, yielding the velocity, pressure variation, and temperature along the pipes and channels in the network.
Cooling of a steering wheel injection mold. The new COMSOL Pipe Flow Module
allows for efficient simulation of the cooling channels using 1D pipe non-isothermal
flow. This is fully coupled to the heat transfer simulation of the mold and
polyurethane part, which was imported as a CAD geometry.
Corrosion Module
Corrosion is everywhere, but is an especially important concern for off-shore structures, ships and submarines, aerospace, and automotive parts. George F. Hays, director general of the World Corrosion Organization, estimates that 3% of the world’s GDP is lost every year due to corrosion. (See the report “Now is the Time”)
This screen shot shows an oil rig structure immersed in seawater and protected
by 52 sacrificial aluminum anodes. Before deploying the anodes, engineers would
use the new COMSOL Multiphysics Corrosion Module to optimize the position
of each anode for the best possible corrosion protection. Visualized is the electrolyte
potential on the surface of the structure.
Galvanic corrosion of a magnesium alloy (AE44) connected to mild steel in a
salt-water solution. The electrode material removal is represented with a moving
mesh, an important variable to be considered when performing such simulations.
The new COMSOL Corrosion Module offers specialized user interfaces to model the electrochemical processes that lead to corrosion. Using the Corrosion Module, engineers who want to mitigate these processes can gain insights into how structures might corrode under certain conditions and how structures can be protected. The module includes the physics required to model galvanic, pitting, and crevice corrosion as well as cathodic and anodic protection.
For more information on COMSOL Multiphysics version 4.3, please visit COMSOL.
Sources: Press materials received from the company and additional information gleaned from the company’s website.
Subscribe to our FREE magazine,
FREE email newsletters or both!Latest News
About the Author

DE’s editors contribute news and new product announcements to Digital Engineering.
Press releases may be sent to them via [email protected].
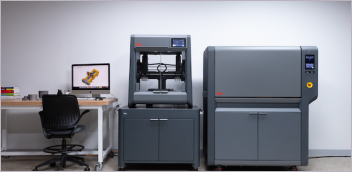
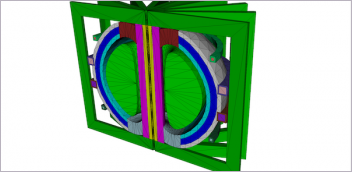
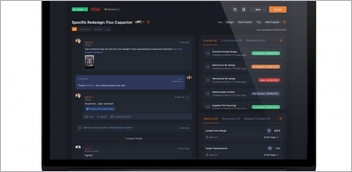
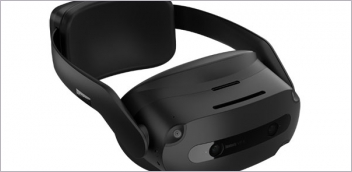