Latest News
November 2, 2007
By Lynn Manning
![]() adidas achieved significant design cycle reduction for its ForMotion line of shoes by coupling surfacebased MCAD with Abaqus finite element analysis (FEA) software from SIMULIA. A unique sliding platetechnology in the heel of the shoe absorbs shock in three directions. |
But consumers who actually run in their shoes — recreationally or professionally — will be pleased to hear that the designers and engineers at adidas are paying attention to a lot more than flashy exteriors. They know that shin splints, a twisted knee, or one bad turn of the ankle can ruin a runner’s season.
Using materials science, biomechanics, and finite element analysis (FEA) simulation, adidas is building motion-responsive, stress-reducing technologies — similar to those found in earthquake-resistant buildings and car stability systems — right into the heels of their running shoes. The shoes still look good, of course. But the best parts now are those you can’t see.
Simulation software is key
Historically, new athletic shoe models were based on retooling existing ones, necessitating time-consuming rounds of real-world prototype testing and redesign. But in creating its new ForMotion line of running shoes, adidas shaved significant time from its design cycle by coupling its surface-based MCAD program using Abaqus/Explicit and Abaqus/CAE FEA software from SIMULIA of Providence, RI.
“If you were going to retool and test a whole new shoe it could take six to eight weeks,” says adidas Mechanical Engineer Tim Robinson. “But when you run simulations it only takes a few days. In terms of speeding up the entire development process, the FEA software has proved invaluable.” Robinson is part of the adidas innovation team, which is made up of designers and engineers both in adidas’ birthplace outside Nuremberg, Germany, and in Portland, OR.
Unique sliding plate technology
A key in the development of the brand’s ForMotion line of running shoes is a component comprised of a pair of sliding polyamide plates and a spherical bearing located in the heel of the shoe. Depending on the model of shoe, a thin polymer seal and sometimes also polymer springs and washers provide stiffness to the system. According to Robinson, the unit adjusts to shock horizontally and rotationally as well as vertically. Designers also felt the unit should decouple the heel to slow “sole-angle velocity” (the speed at which toes slap the ground after a heel makes contact) to help prevent a runner’s common complaint of shin splints.
![]() These External side view strain-contour plots generated with Abaqus/CAE show the results of a biomechanical loading of the heel unit. On the left is the undeformed state and at right is the deformed state. In the first round of virtual prototypes, this information warns the engineers about areas that could be prone to excessive strain and lets them modify the design accordingly. Forces fromthe FEA outcome compared to mechanical tests show a high degree of correlation. |
The sliding plates can also rotate to counteract pronation, which is the amount your foot rolls in with each step and a cause of knee injuries. And finally, the unit automatically adjusts to each individual foot strike to perform the same no matter how far out of line a runner’s foot angle might be.
Turning the concept into reality
adidas designers started out by using their surface-based CAD program because of the design freedom it allowed when dealing with organic geometry. From the CAD models, 3D meshes created in Hypermesh are imported into Abaqus/CAE. “We create the modeling interface and then use it to apply boundary conditions and material properties to the mesh, and tie everything together defining contact, friction, connectors, and other factors,” says Robinson. “Then we solve it using Abaqus/Explicit.”
Material characteristics come from custom libraries that adidas created based on its proprietary materials. Biomechanical data, the basis of the boundary conditions, are equally confidential; they are generated in-house using a Vicon motion-capture system of tiny markers placed at strategic points on a human runner, which are then tracked using infrared cameras as the person moves.
Seeing inside the virtual shoe
Abaqus/CAE is used in postprocessing as well because engineers look for areas of strain and friction by applying simulated horizontal and vertical forces.
“At this stage of development it’s definitely very useful to be able to ‘see’ inside the actual shoe,” says Robinson, “and even cut through the modeling for a closer look, especially when we’re dealing with a complex unit…. It greatly helps communication with our designers about any changes we recommend.”
![]() This model of a leg shows how rotational knee loads are generated by foot impact.The boundary conditions adidas uses are based on biomechanical data generated in-house on acustom testing device. |
Since human feet — and bodies — come in many different sizes, an important part of FEA modeling is sizing and grading the units. “From our biomechanics results we have data about the correlation between shoe size and average weight,” says Robinson. “The radius above the ankle joint will change with a larger size. We use this relationship to functionally grade the shape of the plates, employing FEA to predict the optimum stiffness of the heel unit required for each shoe size.” The shoes also come in four variations with features for control, cushioning, trail running, and competition.
Testing, testing
When prototypes are ready for testing, an adidas test device connected to workstations running FEA software, is used to measure the horizontal stiffness of the ForMotion shoes. The shoe is held at an angle of 30 degrees — a typical male foot-strike angle — and a quasistatic displacement is applied to the heel. This non-destructive test is also used later to test the quality of shoes taken directly from the factory line.
At this point there are rarely any surprises, Robinson notes. “Since we’ve already used FEA to run simulations that are comparable to movements of our test devices, we are very confident that when we get the first sample shoes back they will be very close to what we predicted them to be.”
Engineers use another custom device to test wear: Performance Evaluation Test Equipment (PETE). Using captured Vicon biometric input, this device mimics the motion and impact of an actual runner wearing the shoes. Testing runs up to 100,000 cycles, comparable to 1000km of running.
As a result of all this analysis, adidas’ ForMotion line of shoes should take less of a toll on knees and legs. Now that they are better protected, can hips be far behind? “That’s a question for our biomechanists,” says Robinson. “Engineering shoes to work with hips might be next. We are continually making improvements using Abaqus software to advance the science of shoe design.”
adidas, the adidas logo, ADIPRENE, the 3-Stripe trade mark, FORMOTION, and geoFIT are registered trademarks of the adidas Group. All images courtesy of the adidas Group.
Abaqus Unified FEA
SIMULIA
Providence, RI
simulia.com
Lynn Manning is a science and technology writer based in Providence, RI. Send comments about this article to DE-Editorsmailto:[email protected].
Subscribe to our FREE magazine,
FREE email newsletters or both!Latest News
About the Author

DE’s editors contribute news and new product announcements to Digital Engineering.
Press releases may be sent to them via [email protected].
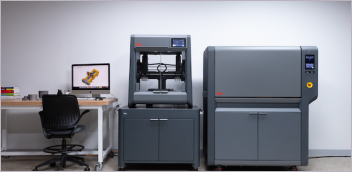
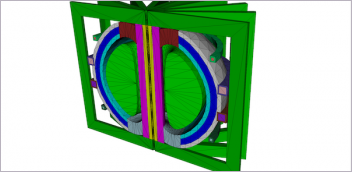
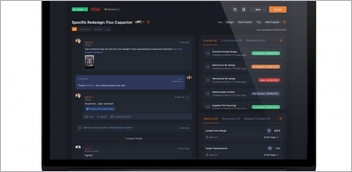
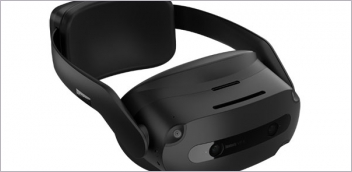