Editor’s Pick: Metal Additive Printer Handles Crack-Prone Materials

The Arcam EBM Spectra H electron beam melting (EBM) metal additive manufacturing system is designed to handle high heat and crack-prone materials including titanium aluminide and nickel Alloy 718. Image courtesy of GE Additive.
Latest News
May 16, 2018
Dear DE Reader:
While working with this guy on an article about developmental research into a life support system for long-term space flight, he pulled out this fascinating metal lattice structure. It was part of a moisture to potable water recovery system. It had been 3D printed with an Arcam electron beam melting (EBM) metal additive manufacturing system. He was excited by the capabilities of the Arcam system, and that unit was an early generation of the technology.
GE Additive recently took the wraps off its new-generation EBM system for metal additive manufacturing, the Arcam EBM Spectra H. Essentially, this high-volume industrial machine is the company's all-new metal manufacturing technology platform. It'll be shipping later this year. Still, this unit has many new and improved features that make it noteworthy right now.
So, what's in it for you? Perhaps foremost, the Arcam EBM Spectra H is designed to enable you to work with high heat and crack-prone materials like titanium aluminide and nickel Alloy 718 at temperatures exceeding 1000°C. This capability could expand your production horizon to include more high-temperature, anti-corrosive components. Aside: The company plans on rolling out additional high-heat materials.
But efficiency is also a big focus here, and it comes in a variety of forms. For one, build speed is up to 50% faster compared with current EBM machines. Reasons for this include a 6kW beam that reduces all pre- and post-heating steps, an improved layering procedure that reduces heating times as well as a movable heat shield that keeps heat in the build area.
Speaking of the latter, the Arcam EBM Spectra H delivers a 9.84x16.9-in. (250x430 mm) build volume. That's about 39% larger than current EBM machines. It's also a dust-tight production environment throughout the process. This helps maintain powder batch integrity while it protects the operator from the powder.
Two, there is lots of automation. For example, automated calibration technology improves the beam position and focus accuracy, which eliminates manual calibration processes. The system features an automated, self-dosing sieve and hopper filling station processes, automatic powder hoppers and automated powder recovery among others.
Today's Editor's Pick of the Week write-up offers some more details on the Arcam EBM Spectra H. Hit the links at the end of the write-up to watch a video on its features and to see a video describing how the process works. It seems a well-thought-out process loaded with potential.
Thanks, Pal. – Lockwood
Anthony J. Lockwood, Editor at Large, DE
Subscribe to our FREE magazine,
FREE email newsletters or both!Latest News
About the Author

Anthony J. Lockwood is Digital Engineering’s founding editor. He is now retired. Contact him via [email protected].
Follow DE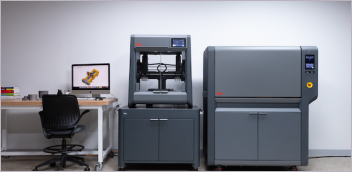
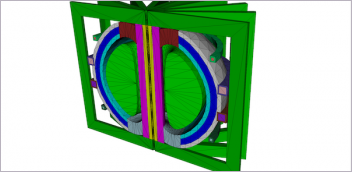
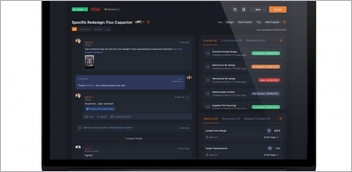
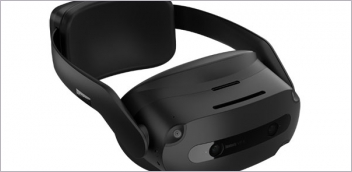