Latest News
December 20, 2007
By Sara Ferris
LFE (Loyalty Founder Enterprise), a manufacturer of metal and plastic electronics enclosures, standardized on PTC Pro/ENGINEER Wildfire 3.0 and PTC Pro/INTRALINK 8.0. LFE reports that its new design processes cut mold design cycle time by 40%.
![]() ![]() LFE manufactures enclosures for electronics devices. |
Founded in Taiwan, LFE has more than 25 years of engineering and manufacturing experience in the metal stamping and plastic injection molding industries. Its major subsidiaries include Axxion Group Corp. in USA, Solleron Corp. in Taiwan, and Loyalty Founder Enterprise Dongguan in China. Today’s increasingly complex product development environment requires LFE to shorten time to market by compressing development cycles without compromising results.
Before choosing PTC, LFE’s non-standardized designing process did not allow LFE’s engineers to effectively analyze key mold design elements. As a result, design errors were often not identified until the physical mold prototype was created, causing rework and development delays. With geographically dispersed clients and teams, communication with clients, or even between concurrent designing teams and departments, was also problematic. LFE needed a solution that could create a common working environment and methodologies to improve engineering efficiency.
After deploying PTC solutions, LFE reduced its mold design cycle time by 40% and elevate overall design efficiency among its engineering teams by 20%. Pro/ENGINEER also enabled LFE to decrease mold design change and BOM list development time. Designs were also quickly reusable, saving critical time that would have previously been spent on redesign efforts.
Pro/INTRALINK enabled centralized vaulting and revision control of Pro/ENGINEER models, relationships and functionality for improved information security and accuracy. LFE was also able to configure the level of access control of its employees for any project and then communicate any changes broadly.
“At LFE, we can support almost any kind of metal stamping and plastic injection design-for-manufacturing (DFM) needs. To fulfill such a promise of product quality to our customers, we have to ensure that for every project, we are able reduce project costs, minimize human error and improve collaboration among different departments to increase operating efficiency,” says Po Hu, general manager, LFE.
Sources: Press materials received from the company and additional information gleaned from the company’s website.
Subscribe to our FREE magazine,
FREE email newsletters or both!Latest News
About the Author

DE’s editors contribute news and new product announcements to Digital Engineering.
Press releases may be sent to them via [email protected].
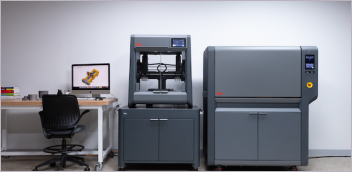
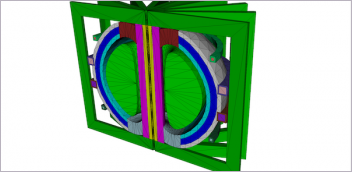
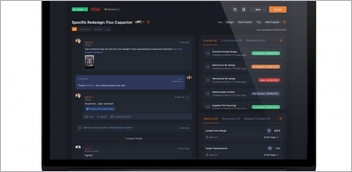
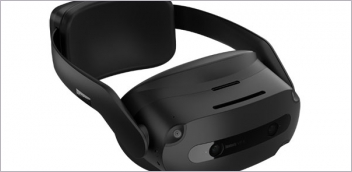