Latest News
February 16, 2017
ESI Group, maker of virtual prototyping software and services for manufacturing industries, has announced the latest version of its PAM-STAMP simulation software for sheet metal forming.

An end-to-end solution, PAM-STAMP covers cold, warm and hot forming processes, and most special processes for all types of metallic materials. ESI PAM-STAMP provides a solution to manage progressive, transfer and line dies, and also tool surface design. From the first feasibility iterations on part design to the final validation of the entire stamping process,ESI Group says PAM-STAMP delivers fast and reliable results, addressing thinning, splitting, compression, wrinkling, trim line optimization, spring back and die compensation, using the company’s Triple Speed technology. ESI PAM-STAMP enables die face designers and sheet metal forming engineers to manufacture parts right first time, according to the release.
“With the latest version of ESI PAM-STAMP 2017, considerable efficiency improvements have been achieved when working with complete line dies,” said Arlem Picinin of AETHRA, Brazil. “It is a huge step forward and makes working with ESI’s sheet metal forming solution PAM-STAMP even more enjoyable and efficient.”
ESI engineers have redesigned the user interface (UI) to reduce the number of clicks and increase work efficiency. Setting up processes is now done directly following a new and streamlined horizontal workflow, facilitating the setup of the entire stamping process; end to end.
Also new in PAM-STAMP 2017, a centralized Operations Manager enables easy definition of the global layout for multiple operations. The stamping process is managed by a new Process Editor. Kinematics can be defined per operation, and users can add, modify, or remove tools.
For more information, visit ESI Group.
Sources: Press materials received from the company and additional information gleaned from the company’s website.
Subscribe to our FREE magazine,
FREE email newsletters or both!Latest News
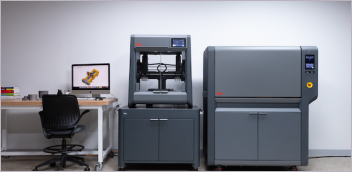
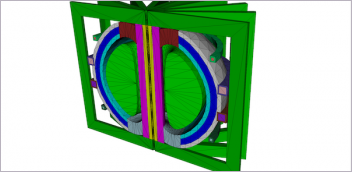
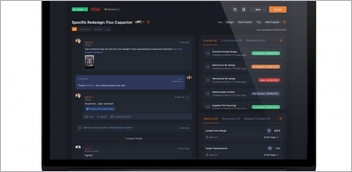
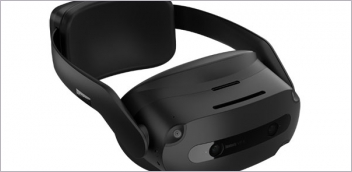