ESPRIT 2009 Introduces a Fresh Approach to Complex 5-axis Milling, 1 in a Series
As multiaxis machine tools become more complex, DP Technology has developed an elegant way to program them.
Latest News
February 2, 2009
By Ann Mazakas
Page 1 | 2 »
![]() 3D features are easily created by using automatic face propagation to select the surfaces tomachine (in green) and the areas to avoid (in red). |
The appeal of multiaxis machine tools is obvious to machine shops of all sizes. These machines typically require only one setup to machine an entire part, saving time and improving accuracy between operations. These advanced machines also have the capability to change the tool axis direction in order to reach machinable areas with shorter, more rigid tools or to reach zones that could not be cut at all with standard methods (undercuts). These benefits make it easy to justify the cost of upgrading to the latest technology.
Usually this type of machine tool has two additional rotary axes incorporated either in the table that supports the part to be machined or on the tool head itself. The challenge is to generate CNC programs that fully exploit these additional axes in an efficient manner. In recent years, the growing complexity of this simultaneous machine movement has made this difficult because of both mathematical and technological challenges.
In addition, any software product designed for multiaxis machines must be easy-to-use and error-proof. The smallest programming error can generate costly damages because the materials, high-precision tools, and accessories for these advanced machine tools are quite expensive.
An Elegant Solution
Based on these premises, the challenge for CAM software developers is how to combine a set of powerful programming functions with a programming process that is easily understood by the user. The capabilities of these functions must be presented clearly, stepping the user through the programming process in order to avoid errors during toolpath definition, while never becoming rigid or imposing limitations.
![]() Five machining patterns are available that range from a standard offset of the boundary to parametric patterns that use the flow lines of a surface as well as patterns created by intersectionof the part and a set of user-defined planes that can follow a linear or curved path. |
The latest release of ESPRIT, a high-performance computer-aided manufacturing (CAM) system, introduces a new concept in highly advanced machining functionality based on the idea that any five-axis machining function, no matter how complex, can be defined with a few simple steps.
This patent-pending technology in ESPRIT 2009 eliminates a problem commonly found in CAM systems, which is the conflict between powerful functionality and the ease with which it can be used.
In the past, CAM software developers resolved this conflict by fragmenting their product into various dedicated functions for very specific types of toolpaths in order to keep a reasonable number of options. A point of pride for some CAM systems is the large number of functions available. The price often paid for this type of software development is that soon the system becomes a labyrinth of functions with the typical end user knowing and exploiting only a limited number of them. Busy CNC programmers cannot possibly be expected to memorize the purpose of dozens of functions in a CAM system. Programmers typically stick to the functions they know best and ignore the rest.
Instead of fragmenting the advanced five-axis functionality added to ESPRIT 2009, the new 5-Axis Composite Milling cycle follows the same logic that machinists themselves use when deciding how to machine a complex five-axis part. Users are presented with a programming process that is familiar and easy to understand, not an overwhelming array of options that may or may not apply to the current machining situation.
By simplifying the methodology of multiaxis machining into one unique function, the user quickly becomes adept at exploiting the full power of the product. With this new approach to CAM functionality, maximum flexibility and compactness can be achieved in the field of five-axis machining definitions.
![]() Four tool-orientation strategies give the user complete control over the orientation of the tool in relation to the part. Here, the tool is forced to pass through a selected point and is limited in itsangle rotation to match the limits of the head rotation on the machine. |
One Composite Function =Multiple Ways to Machine
The 5-Axis Composite Milling function is unique in that it separates the desired shape of the tool path on the area to be machined from the rules that govern the orientation of the tool axis during machining.
The Composite function is based on the idea that every milling job, no matter how complex, can be simplified into four well-defined steps:
• Define the area to be machined
• Define the shape of the tool path on the area to be machined
• Decide how the tool will be oriented as it follows the tool path
• Specify how the tool should move at the beginning, end, and in between cuts.
Page 1 | 2 »
Subscribe to our FREE magazine,
FREE email newsletters or both!Latest News
About the Author

DE’s editors contribute news and new product announcements to Digital Engineering.
Press releases may be sent to them via [email protected].
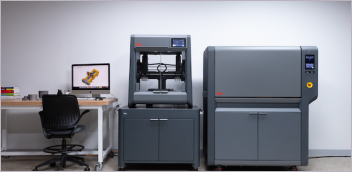
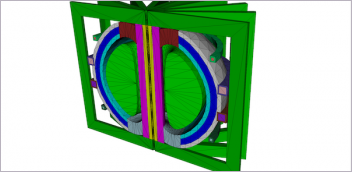
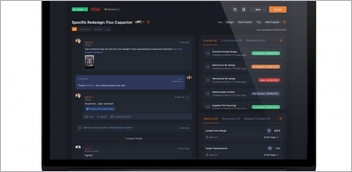
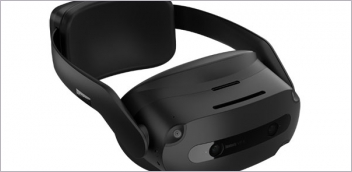