
The R-Series Model RD4 sensor. Image courtesy of MTS Sensors.
Latest News
June 1, 2016
By Matt Hankinson
In industrial-scale sawmills, dozens of machines debark, cut and sand lumber at intense speeds. As the demand for engineered wood grows, these Composite Panel mills face increasing pressure to maximize space and cut costs while maintaining a safe workplace. To meet these needs, engineers at Arauco, a leading producer of engineered wood products, have implemented some new solutions.
“Our goal is to provide the best possible product while meeting the unending demand for engineered composite wood products such as fiberboard and particleboard,” Rusty Wrenn, regional process engineer, explains. “We are always looking for new ways to make our systems more efficient and safer.”
One of Arauco’s more recent advances is the change they made to their Forming Lines feeding the press machines. These machines use 32 worm screws to ensure proper placement of Deckel walls, precise placement of which is required to ensure product quality and production speeds needed to meet industry demand.
In the past, these worm screws would have to be positioned prior to every run, but the encoder at the front of the forming line did not provide accurate position.
“In our industry, positioning is a big deal,” Wrenn said. “In addition, the possibility of a Deckel wall not in position could, and has, caused build up that in turn has cut the forming line belt. The forming line belt is approximately 250 feet long and the very expensive to replace. That is why, a few years ago, we started looking at solutions that would help us know the exact position of each Deckel wall in these machines.”
To address the situation, Wrenn and his colleagues looked for better solutions with sensors attached to the worm screws. Historically, the encoder used to measure the position of the Deckel walls was only at the front of the forming line. Using only one encoder and cable system to send a signal back to the control room increased the likelihood of damage, failure, and wear on the forming belt.
Arauco replaced the traditional encoder system with a Temposonics R-Series Model RD4 sensor from MTS Systems Corp., Sensors Division. In doing so, it eliminated downtime and expense associated with changing this belt prematurely due to damage. Now, RD4 sensor data and electronic control systems from Allen Bradley Controls are used to ensure consistent and easily configurable machine operations. The 32 sensors are connected using an Ethernet/IP network, meaning the Deckel walls are controlled as one unit.
The R-Series
Model RD4 employs MTS Sensors’ proprietary Temposonics magnetostrictive position sensing technology. The sensor consists of a ferromagnetic waveguide, position-determining permanent magnet, which is mobile, a strain pulse converter and supporting electronics. The mobile magnet is rigidly connected to the object of position measurement. It generates a longitudinal magnetic field at its location on the waveguide. A short current pulse is generated by the sensor element and this is passed through the waveguide. As this pulse travels along, it carries a radial magnetic field with it. When the pulse comes into close proximity with the mobile magnet, the two magnetic fields interact with one another. Magnetostriction causes the waveguide to be distorted elastically and this results in the generation of an ultrasonic torsion wave that travels back down the waveguide. When the wave reaches the end of the waveguide it is converted into an electrical signal. As the ultrasonic wave maintains a constant speed traveling along the waveguide, the exact position of the mobile magnet that created it can be determined (given the correlation between the magnet position and the time between when the current pulse was generated and the arrival of the ultrasonic torsion wave in response). Since the output from the sensor corresponds to an absolute position rather than a relative value and the sensor element does not come in contact with any moving parts, there is never any need for recalibration
With the R-Series Model RD4, the sensing element is connected to the electronics via an integral cable. A separate cable connects the sensor electronics with the controller. The electronics housing, along with its mounting block, can be configured with either a side or a bottom cable connection. The electronics communicate data to the control center via an Ethernet/IP protocol, which was developed by Rockwell Automation and is managed by the ODVA (Open DeviceNet Vendors Association).
Arauco uses these systems in their Bennettsville, SC, facility. Since installing the new sensors, the company has saved considerably due to the elimination of downtime associated with replacing the forming line belt, fewer failures due to a cut belt, and easier installation when upgrading.
Composite Panels have often been at the forefront of technological advancements, prompting the introduction of thousands of new methods and machines dedicated to the processing and shaping of wood products. Arauco, with the help of engineering-focused partners, is keeping that tradition alive through the implementation of safer, more productive machines and systems.
More Info
Subscribe to our FREE magazine,
FREE email newsletters or both!Latest News
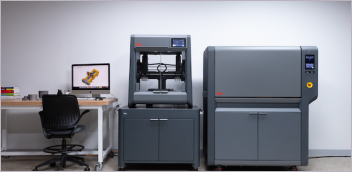
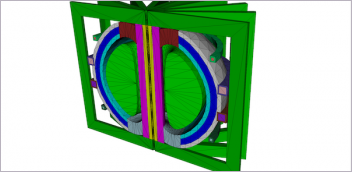
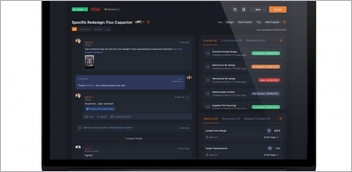
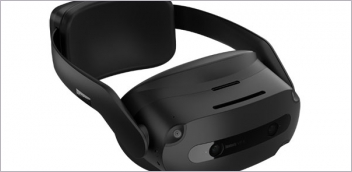