Fast App: 3D Engineering Produces a ‘Supercar’
Creaform stepped up to the challenge of designing an automotive masterpiece with its Handyscan 3D line.
Latest News
September 1, 2010
By DE Editors
All design begins with an idea—but giving shape to that idea is often akin to walking on a tortuous path through thorny underbrush.
![]() |
Car industry veteran Luc Chartrand founded HTT Technologies Inc. in 2000 to pursue a single goal: to make a car that would “represent perfection in its design and its mechanical architecture.” As a specialist in composite materials and a master at replicating exotic cars for the movie industry, Luc built a team of engineers and specialists and got to work.
From a scale hand-made design to a Styrofoam replica, the Pléthore LC-750 was taking shape. The team worked on their prototype for four years, carefully building an entire functioning car, from tires on up, by hand. The car was first presented at the Montreal Car Trade Show on January 19, 2007. As the round of trade show unveilings and press conferences continued, HTT was getting ready to move on to the production line.
|
That was when that thorny underbrush became much denser. Traditionally, obtaining production-line moulds involves taking the prototype completely apart—and ultimately, destroying it. However, the prototype was still needed for further unveilings at several car shows and events. The car had been created physically from the onset, and there were no CAD drawings made during the process. The HTT team members were also keenly aware that should their single, unique prototype be damaged or worse during transport, they would have to start from scratch.
Reverse Engineering a Supercar The 3D model appears in real time on a computer screen, allowing the user to make certain all the required information has been acquired. The Handyscan 3D scanners output an STL file; this format describes a raw, unstructured, triangulated surface by the unit normal and vertices of the triangles using a 3D Cartesian coordinate system—ready to be processed using many reverse-engineering CAD software packages. |
The HTT team knew that getting a CAD model of the Pléthore would solve all the problems they were facing in one stroke. The challenge was to obtain such a CAD model.
The challenge was tailor-made for the team at Creaform, the engineers and technicians who use the 3D scanning technology developed by the company and offer turnkey design and engineering services. The HTT Pléthore design would be in expert hands, even though logistically, the scanning schedule would be tight: The single existing model of the Pléthore LC-750 was due to appear at another event, this time in Europe; the team managed to set aside two days of availability for scanning.
Three applications specialists from Creaform paid a visit to the car builder’s facility. They brought with them three Handyscan 3D laser scanners—one MAXscan and two REVscans.
The MAXscan scans a part in 3D just like the other scanners of the Handyscan 3D line; however, it is a two-in-one tool because it also includes photogrammetric functions. A photogrammetric model is created using special positioning targets. All Handyscan 3D scanners can work together and acquire data simultaneously in the same session, so once the photogrammetric model was established for the Pléthore, the applications specialists linked up the REVscans and completed the scan using all three units. This method can considerably shorten the amount of time required to scan a part as large as an entire car.
The prototype car was known to lack longitudinal symmetry because it had been hand-made; obviously, these imperfections would have to be corrected to make the production version true to the original vision of aesthetic perfection. And as an interesting departure from the usual automotive norms, the Pléthore was designed with the driver sitting between the two passengers. The right-hand side of the prototype was scanned, because it was deemed the most accurately fashioned, along with the front and rear bumpers.
In addition, because scanning does not require total immobility, HTT staff could (and did) continue prepping the handmade prototype for its next showing throughout the scanning session.
From Scan to Supercar
After two days, with the scan data acquired and secured, the Pléthore could continue on its introductory tour while Creaform engineers got to work.
![]() Using the bumpers, a symmetry axis was determined, and a mirror image of the right-hand side was flipped over along that axis to create a perfectly matching left-hand side. |
First, the scan data was processed under Geomagic to clean up the surface mesh. The resulting STL file was then imported into the CATIA v5 REE reverse engineering module and completely reconstructed into a class-A surface. Such attention to detail ensures the moulds created from the 3D plans will require less buffing to create a perfect part.
Next, the complete car had to be recreated symmetrically from its right-hand side. Using the bumpers, a symmetry axis was determined, and a mirror image of the right-hand side was flipped over along that axis to create a perfectly matching left-hand side. This last step usually takes all of 30 minutes.
Finally, minute corrections could be brought to the original design, per requests from the client. HTT could now rely on perfect 3D files of the original Pléthore LC-750, along with the corrections and improvements brought to the design.
The HTT situation was a classic example of reverse engineering calling for 3D scanning expertise. The Creaform team has a very simple strategy in such cases: 1. Use the Handyscan 3D scanners to create a complete computerized 3D polygon mesh of the surface of the object. |
“We are aware that the direct costs of using 3D scanning and engineering to reverse-engineer our car were somewhat greater than those of the traditional method of creating moulds out of the physical parts of the prototype,” notes Sébastien Forest, CEO for HTT. “The long-term benefits of having access to perfect 3D models of the car are so huge, though, that it was well worth the extra cost. The investment was already justified after making only five adjustments to the original design.”
In this decade of 3D technology, CAD models are fast becoming ubiquitous. Under certain circumstances, however, like fitting legacy parts or working with hand-built works of art, the original idea took form in the physical world. In such instances, 3D scanning and reverse engineering become the choice tools to make certain the path is not so tortuous after all—and that thorny underbrush does smell sweet.
The prototype was built and outfitted with its signature V8 engine, and Chartrand took it for a zip around the test track as soon as it was ready. “Driving a car I actually designed from the ground up was very special,” Chartrand says. “The central driving position gives the impression of driving a single-seater race car, even with passengers on both sides! It’s really a completely different type of vehicle.”
More Info:
Creaform
Geomagic
HTT Technologies
Subscribe to our FREE magazine,
FREE email newsletters or both!Latest News
About the Author

DE’s editors contribute news and new product announcements to Digital Engineering.
Press releases may be sent to them via [email protected].
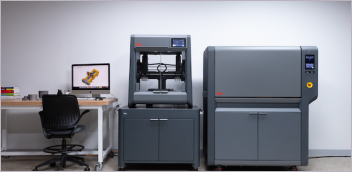
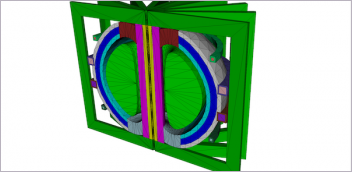
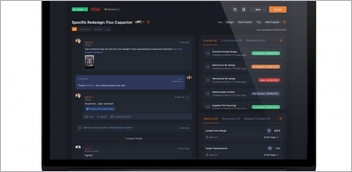
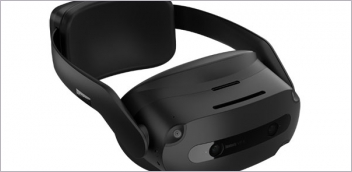