Latest News
June 14, 2012
By DE Editors
Heiner Philipp has worked as a mechanical engineering consultant for nearly 20 years since graduating from the University of Windsor with a bachelor’s of science degree in engineering. His company, Southwinds Engineering Inc., is based in Flesherton, Ontario. Philipp’s areas of expertise include machine design, design for manufacturing, automation design and fabrication and the Ontario Building Code.
![]() |
Crane body fitted to a straight truck. |
Phillipp has been a KeyCreator user since 1989, when he was first exposed to the software in college. Over the years, Philipp has done a number of projects for Wilcox Bodies Ltd., a company that specializes in manufacturing custom service, utility, crane bodies, emergency rescue vehicles, tool boxes and diesel tanks made out of steel and aluminum. The company asked him to assist in making one of its products, a crane body for trucks, lighter, simpler and less expensive to build.
![]() |
Physical testing of new design. |
The custom crane body is attached to the back of a 3- to 5-ton truck, and is used for servicing off-road equipment, such as bulldozers and excavators, with parts like engines and brakes that are too heavy to be removed by hand. The original crane body design used a structure made of tube steel, angle iron and steel plates that fit inside a non-structural cabinet on the back of the truck. The structure connected to the crane, to the frame of the truck and to outriggers that are lowered to the ground when the crane is in use to prevent the truck from tipping over.
Philipp’s idea was to make the box itself structural and eliminate the need for the other structural components. But he knew the crane body manufacturer would not want to go to the expense of building and destructively testing the new design unless he could first prove it would work and save money.
In the past, his only option would have been to spend several weeks creating the geometry for the new design and manually meshing and analyzing it with FEA software. This would have taken longer than could be justified by the size of the job, so it probably would not have been practical to evaluate the new design using traditional methods.
Instead, Philipp used Kubotek’s KeyCreator Analysis, FEA software that integrates with KeyCreator CAD software to define and optimize the new design concept in just a few days. The customer provided the original design of the crane body as a SolidWorks CAD file. Philipp used KeyCreator direct modeling CAD software to open the native SolidWorks geometry provided by his customer. Opening the geometry in KeyCreator freed him from the constraints of parametric CAD, so he could quickly modify the existing geometry to create his new design.
“KeyCreator has always offered direct modeling, which the rest of the CAD software developers are now going back to because of its ability to work around many of the strangleholds of parametric CAD,” Philipp says. “I work for many different companies, and with KeyCreator I can work with their files as easily as I can work with files that I have created myself.”
Philipp used KeyCreator’s interference check feature to look for overlaps or gaps that would interfere with the analysis. The software highlighted several overlaps, and Philipp corrected them by cutting away excess material. Then, Philipp began the structural simulation. Rather than transferring the geometry to a different environment for finite element analysis, he used KeyCreator Analysis to quickly convert the geometry and automatically apply a finite element mesh, using features that allowed him to control the mesh density to deliver the required level of accuracy while minimizing solution time.
![]() |
The load in the new design simulation is twice that of the old design simulation, yet has lower stress, as can be seen visually. |
“The automatic meshing in KeyCreator saved me a week’s worth of manual mesh creation that I would have had to go through using my old FEA program,” Philipp says. He added material properties, including the welds, and then added constraints to the model to represent how it is supported and what loads are applied to it. He applied a load of 4,400 lbs. at 10 ft. from the pivot point of the crane, or 44,000 ft.-lbs., which is the maximum capacity of the crane. He fixed the crane body to the truck frame, and the outriggers in turn were fixed to the ground.
With the FEA setup completed, Philipp entered a few more parameters on the feature tree to analyze the concept design. KeyCreator Analysis uses strain-enriched FEA (Sefea) technology to produce accurate results with a less-dense mesh—in less time and with fewer memory resources. The analysis results, including stresses and deflections, were plotted directly onto the original design geometry within KeyCreator, making them easy to interpret.
Philipp wanted to keep the stress at 50% or less of the yield stress, the point at which the structure starts to deform. The deflection values were not a concern in this application because they were well below the yield limit.
The results showed a few areas where stress levels in the structure were above the 50% level. Philipp either increased the thickness of the box or added a strut or corner support in these areas. In other areas where stress was at low levels, Philipp reduced the thickness of the box, and removed struts or corner supports to reduce weight and cost.
![]() |
The old design. |
“Within a couple of hours, I had refined the design to the point that I was confident that it would provide the required safety factor, and the cost and weight of the structure were near or at optimal levels,” Philipp says. “I then turned the design over to my customer and provided them with specifications on what types of steel, welding techniques and methods of inspection should be used. The customer built a prototype and tested it to failure to validate the design. The new design failed at only 5% above the level predicted by the simulation. We were very pleased with these results, since they were within the engineering material tolerance.”
The new FEA-optimized design reduced the cost and weight of the structure by 40%, while increasing storage capacity by 15%.
“In the past, this design might never have seen the light of day because it would have taken several weeks to define its geometry and analyze it using conventional structural analysis tools,” Phillipp concludes. “The release of KeyCreator Analysis integrated with KeyCreator CAD software makes it easier and faster to optimize any mechanical structure. KeyCreator Analysis is also supported by the same excellent technical support team that I have found to be capable of resolving any problem very quickly. My relationship with Kubotek has been fantastic for the past 23-plus years.”
Info
Kubotek: KubotekUSA.com
Southwinds Engineering Inc.: SouthwindsEngineering.ca
Subscribe to our FREE magazine,
FREE email newsletters or both!Latest News
About the Author

DE’s editors contribute news and new product announcements to Digital Engineering.
Press releases may be sent to them via [email protected].
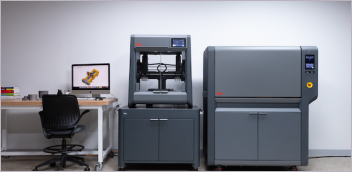
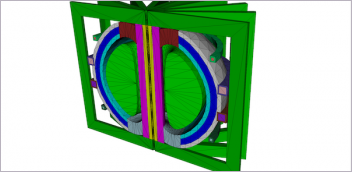
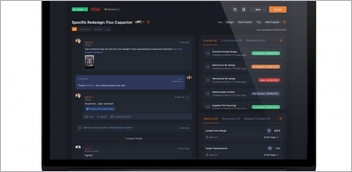
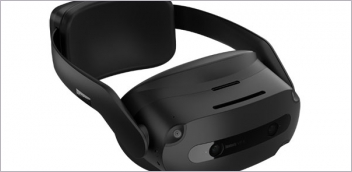