Fast Engineering for Winning Cars
Data integration cuts time spent designing Formula One racecars.
Latest News
October 14, 2007
By Sara Ferris
Red Bull Technology (Milton Keynes, United Kingdom) provides design and manufacturing services to Red Bull Racing and Toro Rosso, two Formula One racing teams sponsored by the Red Bull energy drink company. To assist in designing, testing, and manufacturing its racecars, Red Bull Technology has assembled an array of state-of-the-art design and manufacturing tools. The company is always seeking new ways to capture and use product knowledge to help make better decisions.
![]() The Red Bull Racing team’s Formula One racecar was developed entirely in software. |
Formula One cars are made up of around 7,000 parts, many of which use advanced technology. Most parts (close to 90 percent) are designed anew each season, and many parts undergo further updating during the racing season, which spans 17 races in nine months.
Designers must work within strict rules and meet tight deadlines, as the racecars must be ready to roll on race day. Integrating the many disciplines involved in the process helps Red Bull Technology meet these challenges.
The Combination of Technologies
The Red Bull Racing team’s current Formula One car was developed entirely in software, beginning with a definition of functional requirements and Formula One regulations and proceeding to an assembly tree and geometric part models for the entire vehicle. The company used UGS NX to model the car and required tooling, as well as to perform vehicle dynamics simulations and stress analysis. Teamcenter handles document management and collaboration.
An IBM cluster is dedicated to a computational fluid dynamics (CFD) analysis of aerodynamics, supplemented by wind-tunnel testing of prototypes.
To provide the design team with quicker access to wind-tunnel test results, Red Bull Technology uses a portable coordinate measurement machine (CMM) from Leica Geosystems, a company that is now owned by Hexagon. The LTD800 Laser Tracker and portable T-probe are built into the company’s new wind tunnel (the company has two). Before, Red Bull Technology used height gauges to set up the racecar in the wind tunnel, a process that took two hours. With the CMM, it takes 20 minutes to set up the car. With around 12,000 testing sessions per year, the time saved added up quickly.
![]() |
The Leica system provides accuracy levels of within 0.1 millimeter. Another advantage to using the CMM is that any changes made to the model car during testing can be recorded and transferred back to the original CAD model.
The laser trackers are also used for tool and composite component inspections, car legality checks, and specific car measurement checks.
CAD, Data, Scan, and Reports
Red Bull Technology makes around 80 percent of car components in-house. Metal parts are machined directly from CAD models. All parts made are subject to rigorous inspection and quality checks. For this purpose, the company recently added two global CMMs from Hexagon Metrologyof Rhode Island.
The two bridge-type machines — a Global 7105 Performance and a Global 7107 Advantage — run Hexagon Metrology’s measurement and inspection software program, PC DMIS CAD++. PC-DMIS Direct CAD Interfaces communicate directly with UGS NX to provide offline programming capability.
The technology package also includes Hexagon Metrology’s TESASTAR probe heads fitted with touch-trigger scanning probe kits for the geometric measurement and inspection of complex surfaces. The kits’ analog scanning sensors will provide Red Bull Technology with tactile data collection in point-to-point and continuous-path modes.
Red Bull Technology will use the new technology to generate inspection part programs in advance of the arrival of components. The goal is to reduce lead times and CMM bottlenecks.
“We chose Hexagon because we needed to refine our process and deliver accurate, clear, easily understood, and concise reports,” says Red Bull Technology Quality Manager Chris Charnley.
Red Bull Technology typically builds five chassis per season. Cars are inspected and rebuilt after every event. Work continues at each race, with simulations and track testing to find the optimal car setup. Performance data and faults are transmitted back to engineering, and stock information goes to manufacturing.
While the coordination of all these processes is what management is about, it’s quite possible that the design benefits coupled with savings in effort, time, and cost may produce a winner.
More Information:
UGS
Plano, TX
ugs.com
Hexagon Metrology
North Kingston, RI
hexagonmetrology.net
Leica Geosystems
St. Gallen, Switzerland
leica-geosystems.com/metrology/
Contributing Editor Sara Ferris has covered the CAD industry since 1995. She was formerly editor-in-chief of Cadalyst magazine. You can e-mail comments about this article DE-Editorsmailto:[email protected].
Subscribe to our FREE magazine,
FREE email newsletters or both!Latest News
About the Author

DE’s editors contribute news and new product announcements to Digital Engineering.
Press releases may be sent to them via [email protected].
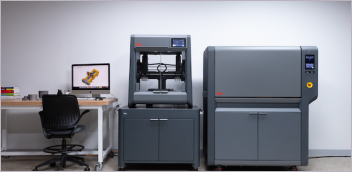
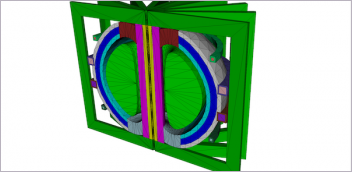
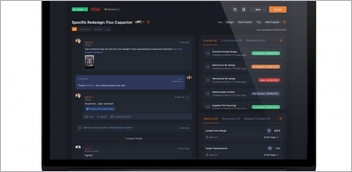
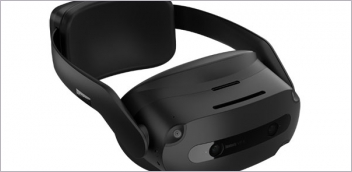