Latest News
January 14, 2015
By David Souders
Editor’s note: This article was submitted on behalf of Flow Science Inc., makers of FLOW-3D.
When you’re analyzing the hydraulics of a flood-control system and the entire project has a six-month turnaround, you want a CFD (computational fluid dynamics) solution that’s accurate and fast. When you need to evaluate thermal characteristics of dozens of possible metal mold designs in just a few days, you need a CFD solution that’s easy to change and optimize. And when you need to share the results of a hundred shape variations of an inkjet print-head nozzle with manufacturing, purchasing and quality assurance, you need visualizations that reveal the finest details.
FLOW-3D CFD software from Flow Science, now in version 11, addresses these various needs with speed, accuracy, clarity and high productivity functions. As a multiphysics package, this platform offers a wide range of models to suit each operational scenario (e.g., free surfaces, turbulence, multi-phase flows, porous media and more) and the company’s unique Fractional Area-Volume Obstacle Representation (FAVOR) approach accurately models 3D flow while using compact computational resources. The software’s modeling techniques simulate models at scales ranging from micro-fluidic dispensers and automotive fuel tanks to high-pressure dies and tsunami waves. Version 11 introduces several major improvements including enhanced meshing, remote solving and a completely new customized post-processor.
Visualizing Volumes, Splitting Screen-Views and More
Seeing deeply inside a flow simulation, not just viewing its surface behavior can make a big difference in understanding the nuances of fluid flow. FlowSight, a totally new FLOW-3D post-processing and visualization tool, now offers full volume rendering, presenting images that go far deeper than basic iso-surface results. Users can view animated streamlines and interactive 2D slices through both fluid and structural domains and compare multiple simulations simultaneously. A single plot can show flow behavior along with fluid-structure interactions or thermal stress changes and rapidly present large numbers of plots. A quick click puts results into a simple flipbook format.
For users who regularly re-engineer variations of standard product or system designs, FlowSight supports “save and restore” settings for repeating common tasks. A new CFD calculator not only lets users easily multiply, divide and scale existing variables but also define time-averages, integrated values and custom dimensionless parameters.
FlowSight’s new animation possibilities are particularly helpful for non-experts reviewing the effects of different design choices. On a single screen, split windows can simultaneously show different topographical views of the same simulation — for example, a tank filling versus time — with the full 3D geometry, a 2D-clip at the centerline, an elevation view and a top view. Or multiple windows can display different system variables of water flow through a spillway, each tracked on the same timeline: the 3D simulation, entrained air, turbulent kinetic energy and total hydraulic head. All animations are interactive for detailed study at any point. (Editor’s Note: See FLOW-3D examples of mixing-tank simulation, thermal plume analysis, flash flood simulation and more on YouTube.)
Advances in Meshing
Accuracy of a CFD simulation depends on many factors and meshing is one major component. FLOW-3D’s approach to meshing combines the advantages of structured rectangular grids with the flexibility of deformed, body-fitted cells at the fluid-solid interface via its FAVOR method. For many years, FLOW-3D let users mesh adjoining regions or blocks with rectangular grids of varying resolutions within a domain, and now these blocks can be embedded, overlap and conform to specific geometries. The resulting arrangement allows users to locally refine their mesh to capture important phenomena in particular areas while not greatly affecting the computational power needed to resolve an entire domain of fine resolution.

Users have several options to define the conforming regions, combining them with nested or linked areas as desired. For casting applications, the overlapping mesh block would typically be cavity-conforming, since the cavity requires a fine mesh (to model rapid fluid flow) and the mold a coarse one (to model the slower thermal conduction). For fluid flow around a structure (such as ocean waves encountering a pier), a component-conforming mesh block would resolve fine details strictly in the thin interaction area surrounding the solid structure. Users can include part or all of the structure’s geometry in the conforming mesh block.
In blocks with more than two overlapping regions, FLOW-3D solves the flow equations in the one with the finest mesh, based on the average cell size in the block. All cells are still “FAVORized,” meaning that the solution is interpolated between blocks rather than iterated on a solution from one cell to another. By simplifying mesh generation and reducing the number of blocks generally needed in a simulation, these new meshing capabilities reduce computational overhead while preserving accuracy.
GUI Overhaul
The version 11 graphical user interface (GUI) includes a new quality-checking feature that detects resolution issues on imported geometry defined by STL files. Users can load the results into the graphical display window in the Meshing & Geometry tab and perform interactive analyses. Additionally, baffles, history probes, pointers and valves can now be added to a simulation interactively. The materials database has also been upgraded to include more materials and more temperature-dependent properties, as well as to support better navigation and organization.
David Souders is the vice president of Sales, Marketing and Customer Support at Flow Science Inc. in Santa Fe, NM. Currently leading a staff of nine professionals, he has helped to grow Flow Science into a competitive, internationally known engineering software company. He has a B.S. from the University of New Mexico and a M.S. from the New Mexico Institute of Mining and Technology with a focus in fluid and thermal sciences.
Subscribe to our FREE magazine,
FREE email newsletters or both!Latest News
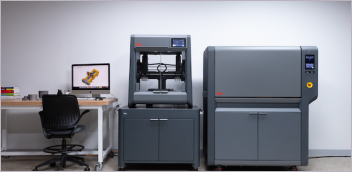
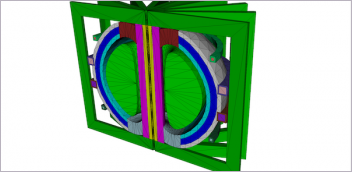
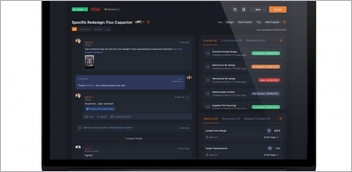
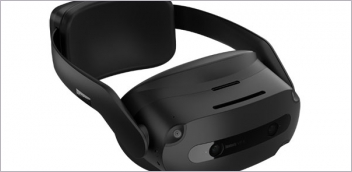