Getting Specific: Exploring Niche Design Analysis Software, 1 in a Series
Part 1: Specialized packages -- computer aided engineering software designed everything from assessing composites to evaluating piping -- zero in on efficiency.
Latest News
November 1, 2008
By Pamela J. Waterman
Page 1 | 2 »
![]() This is an NEi Nastran Tension-Only Quad Element analysis specifically created to model highly nonlinear behavior of load transfers in wing and fuselage structures. (Image courtesy NEi Software) |
How often do you need to tackle shot peening of a turbine blade? Evaluate the safety of a proposed mining excavation? Minimize vibro-acoustic problems in automotive design? If your company focuses on a vertical industry, the answer could be “every day.” For many such challenges, you’ll get the fastest results using software streamlined for your day-in, day-out applications.
Engineers who simulate load stresses on multi-ply tires today will probably not be designing washing-machine gears tomorrow, so specialized software can provide a real boost in efficiency. General solvers certainly have their place, but niche software can work side-by-side with those packages, saving time by offering menus with just the right language and options; no more, no less. This article examines a number of such analysis products as well as some sample “niche” applications that may surprise you with their pervasiveness.
![]() The NEi Tension-Only analysis is used by Cessna. (Image courtesy of NEi Software) |
Focus on Mechanical Stress
Mechanical analysis is the foundation of many engineering design projects. No wonder so many packages have been developed that help users build specific model types and subject them to very specific loads. Sometimes the niche solution is driven by one customer’s needs, which opens up a new problem-solving method for other users.
A chance meeting between engineers at NEi Software and Cessna Aircraft led to the design of a Tension-Only Quad (TOQ) element for modeling the detailed behavior of wing and fuselage structures. In real components, certain areas undergo compression that creates buckling. In the virtual world, there had been no good way to model this highly nonlinear action where the resulting semi-diagonal tension field transfers the load to other structural members.
![]() |
NEi Software solved the modeling problem by incorporating a unique effectiveness factor, allowing the panels to carry both a tension and compression capability as needed. The Cessna engineers found that using this modeling element within an NEi Nastran analysis allowed them to combine six different tail-section models (originally for each of six load orientations) into one. This difference saved a great deal of overhead any time the geometry was changed, eliminating repetitive work functions and reducing the analysis cycle time.
In the case of automotive design, design factors can stem not just from consumer input but from government regulations. ESI Group tackles these requirements with PAM-CRASH 2G, its second-generation analysis package for crash simulations.
![]() A5 Frontal impact of a VW Passat according to Euro-NCAP Simulation and Test, as calculated with PAM-CRASH 2G from ESI Group. The photo shows a comparison to physical crash test results. The PAM-CRASH 2G workflow helps users build their models faster while verifying designs against government regulation compliance. (Image courtesy of Volkswagen AG) |
Because the federal government defines the pass/fail criteria for automotive crash-worthiness, the end user has limited leeway in design. The actual analysis is based on classic finite element analysis (FEA) of door-facings, padding, seat design, and airbags, but the graphical user interface (GUI) is tailored to the end-application. PAM-CRASH 2G offers a workflow that helps users build their models faster while combining regulatory compliance, standard operating procedures, and best practices.
Designers can quickly set up a scenario where they set the vehicle speed, choose a crash barrier of a certain shape and material, and select one of a number of defined crash-dummies with its own set of parameters. Postprocessing capabilities make it easy to look at the resulting head and neck acceleration that the dummy model experienced. PAM-CRASH 2G simulations even allow for variations in manufacturing tolerances from different casting and forming processes. The results help designers evaluate how such variables as plastic deformation or the thickness distribution on a door panel impacts crash worthiness.
Solving for Mine Safety
Recent tragedies in the realm of mining safety have highlighted the need for improved planning and operations. Abaqus FEA software from SIMULIA, the Dassault Systèmes brand for realistic simulation, is now used to analyze models of mines around the world. The goal is to successfully engineer the safety and productivity of planned deep-mining operations.
Using measurements of site deformation and seismic activity, Abaqus FEA models have been calibrated, and in a single day, used to simulate a full, 3D inelastic model of a mine’s lifecycle. These models are able to include rock mass volumes spanning several kilometers around an ore body. To understand the effect of seismic events, SIMULIA engineers have developed a targeted Dissipated Plastic Energy (DPE) analysis method. Abaqus can also evaluate the unusual strains and loads involved in mine excavation in order to design appropriate ground supports. Users compare the cost savings and improved safety achievements to those gained through “what-if” crash simulations in the automotive world.
Page 1 | 2 »
Subscribe to our FREE magazine,
FREE email newsletters or both!Latest News
About the Author

Pamela Waterman worked as Digital Engineering’s contributing editor for two decades. Contact her via .(JavaScript must be enabled to view this email address).
Follow DE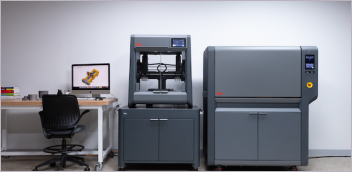
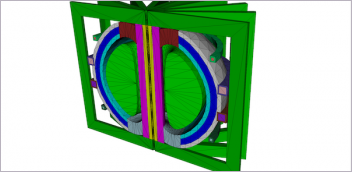
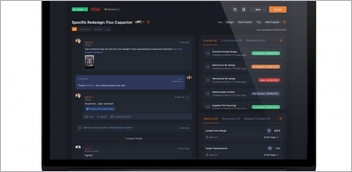
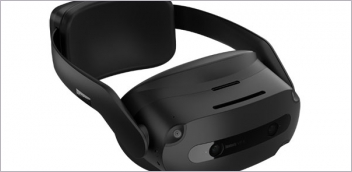