Healthsense Slashes Time-to-Market with Protomold and First Cut Prototype
Latest News
May 1, 2008
By Greg Kagan
![]() |
Mechanical Designer Dave Anderson of Healthsense is a fan of both Protomold and First Cut Prototype®, divisions of Proto Labs. “Three years ago I looked at ProtoQuote®, Protomold’s free online quoting tool,” says Anderson. I uploaded a CAD model and was very impressed with what I got back. Within a day I had a detailed quote along with feedback on the moldability and design of my model. I could adjust parameters like finish, resin, and quantity, and the pricing changed while I watched. And ProtoQuote’s 3D viewer pointed out where I could adjust and improve the design.”
![]() |
Healthsense, located in Mendota Heights, Minnesota, develops systems for senior living facilities providing independent living and assisted living services, along with systems that allow older individuals to stay in their own residences. “Within a care facility, a pendant worn by each resident broadcasts a radio signal allowing the resident’s location to be determined by triangulation across multiple WiFi access points,” says Vice President of Research and Development Dan Vatland. “A push-button request for help is forwarded over the Internet to Healthsense 24-hour data centers and on-site help is dispatched.”
In 2006, Healthsense rolled out eNeighbor, a new platform developed with a grant from NIH. Under this program, sensors are placed around the user’s home to monitor activities. The system watches for anomalies like unusually long periods of inactivity, and can generate a call for help, which is sent to a neighbor. “We first used Protomold with the eNeighbor system,” says Anderson. “We didn’t want to invest in expensive steel molds, but we needed a product we could take to market. Protomold made parts for 1000 pendants, quickly and inexpensively.”
“We started working with First Cut Prototype, Proto Labs’ quick-turn CNC-machining division, when we needed five sets of prototypes for functional testing of a new device,” says Vatland. Their price was reasonable, they could produce parts in one day, and their parts were ideal for functional testing. Their prototypes cost a little more than FDM (fused deposition modeling), but they offer a wide variety of materials, allowing us to perform testing we couldn’t do with FDM. It was a complex design, and along with fit we had to confirm details like water tightness and get feedback on issues like ‘look and feel.’ FDM parts are too rough for a lot of those tests, and SLA (stereolithography) parts are too brittle.”
“We have nothing against rapid prototyping,” says Anderson. “SLA is quick and inexpensive, but you can’t use it for functional testing. And with FDM’s ABS-type material the finer features didn’t hold up. First Cut’s machined parts had no such problems. In the future, we would probably use First Cut for prototypes. Then we would contact Protomold if we needed production parts while we were waiting for high-volume steel tooling. Together, they provide all the prototype and low-volume production parts we need, in a variety of resins at reasonable prices.”
Information:
First Cut Prototype
5540 Pioneer Creek Drive
Maple Plain, MN 55359
P: 763-479-3680; F: 763-479-2679
[email protected]
firstcut.com
Subscribe to our FREE magazine,
FREE email newsletters or both!Latest News
About the Author

DE’s editors contribute news and new product announcements to Digital Engineering.
Press releases may be sent to them via [email protected].
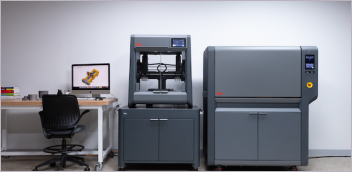
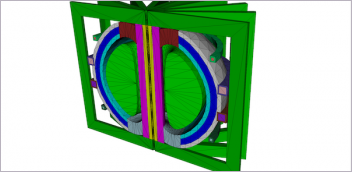
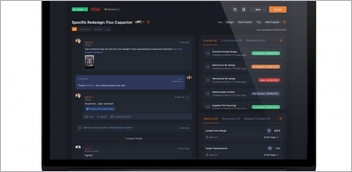
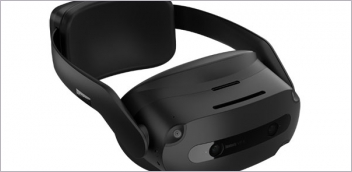