Latest News
December 13, 2007
By Jon Cobb
![]() |
For years, engineers and designers have quickly recognized the value of in-house modeling capabilities. For executives, the appeal of in-house modeling is generally not as immediate, but the value is hard to ignore once shown how it impacts productivity and the bottom line. Steve Robbins made a powerful point in his October 3 DE article titled “It’s All About Rapid” when he noted that what in-house modeling capability means to executives is a “higher return on investment.”
Making the Executive Case for 3D Printing
I would like to share an example that illustrates this point. Recently, Pete Ryan, senior product development engineer for Kirby Morgan Dive Systems requested that the ownership purchase a 3D printer for his design team.
At Kirby Morgan, the design phase is rigorous and central to the company’s identity. The company has a rich history of providing cutting edge equipment and thrives on delivering innovative, fail-safe products to the diving community. From commercial diving helmets to scuba regulators, Kirby Morgan dive systems are frequently designed to accommodate unique diving applications and extreme environments.
Ryan was in search of a more time-efficient process to build accurate, cost-effective 3D models used in the development of its dive systems. By bringing 3D printing capabilities in-house, he sought to cut model production time and to obtain complete control over the product design process. “Dimension was the obvious choice for us,” Ryan said. “The durability and accuracy of the models produced meets our high standards and the purchase price of the Dimension 3D Printer was highly competitive.”
“I pitched the idea of purchasing the idea to our owner and it experienced early resistance due to budgetary issues. The one point that truly resonated with ownership was the fact that bringing a 3D printer would flat out increase productivity, allowing us to move products through design phase and into production faster – increasing profits.”
Ryan’s argument linking the addition of an in-house 3D printer to increased productivity and profitability was a powerful one. The funding was approved and Kirby Morgan purchased a Dimension 3D printer shortly thereafter.
The Dimension 3D Printer Delivers
Kirby Morgan has experienced significant success since the purchase of the Dimension 3D printer. When the U.S. Military requested a modified regulator with a higher level of breathing performance than the standard unit Kirby Morgan was producing, the Dimension 3D printer was put to the test. The design team needed to build and test two new components for the regulator, and the military requested delivery of the regulator as soon as possible.
“Since adding the Dimension 3D printer, we have averaged a 50 percent reduction in time spent on product design. This increase in productivity has had a real impact on the bottom line.”
With the Dimension 3D printer, Kirby Morgan was able to maintain its high standard of quality while meeting the U.S. military’s request for fast delivery. Kirby Morgan created several models of the two new components, evaluated the models, made modifications and had the special regulator finished and delivered to the U.S. military in just one week – cutting weeks off the standard completion time required when Kirby Morgan outsourced 3D model production.
“In the past, we were unable to fill custom product requests in such a short time period,” Ryan said. “The modified regulator we developed for the U.S. military displayed the major speed and efficiency improvements you can achieve with the introduction of an in-house Dimension 3D printer.”
The Dimension 3D printer has consistently provided Kirby Morgan with durable models that can be tested and retested during the evaluation process. The 3D printer also has increased the production team’s efficiency during the design process by enabling them to cut model production time and the time required for the product review process.
“We now have a much higher level of control over the timing of the product design phase,” Ryan said. “Since adding the Dimension 3D printer, we have averaged a 50 percent reduction in time spent on product design. This increase in productivity has had a real impact on the bottom line.”
3D printing delivers bottom line results – now that’s designer speak that any executive can understand.
Dimension 3D Printing Group
7665 Commerce Way
Eden Prairie, MN 55344-2020
888.480.3548
dimensionprinting.com
Subscribe to our FREE magazine,
FREE email newsletters or both!Latest News
About the Author

DE’s editors contribute news and new product announcements to Digital Engineering.
Press releases may be sent to them via [email protected].
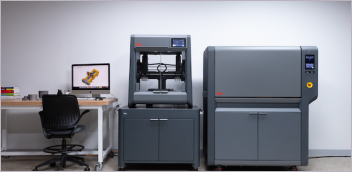
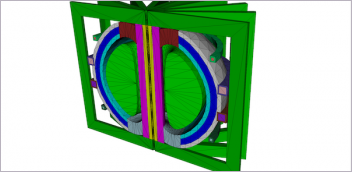
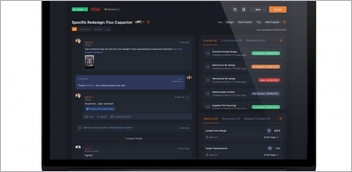
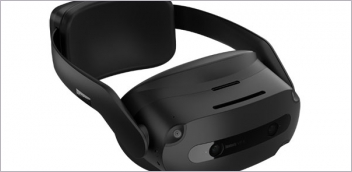