Latest News
December 23, 2014
Interface design is increasingly impacting the success or failure of electronic products, but a well-designed interface is a complicated task. Given the complexities involved in interface design, it is no wonder that today’s product designers and engineers are turning to interface specialists to support their product design.
Whether it is an HMI (human-machine interface) or MMI (man-machine interface), these specialists are experts in dealing with the highest levels of interface complexity, both human and technological.

“There are instances when it is important to work with an interface specialist that has the full capability of supporting you from the ground up,” says Joey Kitabayashi, vice president of Engineering at Capital Cooking Equipment. Kitabayashi adds that the type of control panel can add the need for a specialist supplier; for example, glass touch-capacitive and other panels that require software, which is an additional interface.
The design of the HMI or MMI has made a vital contribution to the success of countless products across a spectrum of industries ranging from the most sought-after consumer products to most business, medical and industrial equipment.
In the case of Capital Cooking Equipment, a manufacturer of high-end cooking indoor and outdoor appliances for residential applications, MMIs are featured on several models of equipment, notably electric wall ovens and dual-fuel ranges.
“These sophisticated products require controls as opposed to just mechanical pushbuttons, knobs and dials,” Kitabayashi says. “Essentially, they require an interface between the operator and the control system to allow various kinds of input.”
To provide customers with a choice of MMIs, Capital Cooking offers some models of ranges with a membrane switch panel composed of deformable switches that connect with the control system. Some of the oven products feature a passive touch-capacitive glass panel that communicates with the control system via software.
To handle the design of its more complex interfaces Capital, Cooking enlisted the expertise of Jayco mmi Inc. With 35 years of experience, the company designs, engineers and manufactures a wide variety of interface products. It specializes in custom control panel assemblies, keyboards, keypads and flat panel (membrane) switches for military, defense, aerospace, medical, security, communications, industrial and commercial applications. It is one of only a few suppliers in the U.S. capable of handling extremely complex design work that utilizes virtually any available interface technology.
“With over 2,000 projects completed, we know that the key to a successful product is to understand the human connection, both with the interface itself, and with our clients and partners,” says Hemant Mistry, president, Jayco.

Kitabayashi has worked with Jayco on interface projects for over 15 years, seven of them while at Capital Cooking Equipment. “Most recently we worked with them on the glass touch-capacitive panel for a residential product. They formed a team with experience in that type of interface, including a software developer to create a program that would ensure that all signals got to their proper destinations,” he says.
Kitabayashi adds that Jayco also performed some fine-tuning to adjust the sensitivity of the glass panel. If the switch settings are too sensitive, then users could set them all off simply by walking past the equipment. However, if the switches — either deformable or glass panel — are not sensitive enough, then they won’t activate or deactivate when necessary.
Developing a successful machine interface involves other design subtleties such as ergonomics, psychology and other “user-centric” considerations. Plus, there is a host of available materials and interface technologies to choose from, a need to perform in harsh environments and, increasingly, the need to fit the most effective HMI within extremely limited space on smaller products.
Whether the interface is displaying information, collecting data or controlling operations, it may require special design considerations such as ruggedized features or the integration of multiple elements. These are indicative of the many design challenges at the higher levels of complexity shared by HMIs and MMIs.
Avoiding Design Pitfalls
With growing demand for more complex software and touchscreen technology, particularly when developing professional equipment for critical applications, designing the most appropriate HMI or MMI is becoming even more challenging in many respects. With such a wide array of available solutions, it is extremely difficult for most product designers to determine which switch and display technologies are appropriate, which control modalities should be used, which functions require direct user access, which materials and construction techniques are optimal and what engineering constraints influence both design and cost.
Still, the product developer may be tempted to design the interface on a build-to-print basis, turning over the plans to an interface manufacturer to build the control panel or keypad or other device.
There are serious challenges involved when customers build-to-print their own interface designs,” says Keith Heinzig, vice president of Engineering at Secure Communication Systems Inc. “Those include possible errors requiring redesign and additional time and money. Also, depending on the application, reliability is always a key constraint.” Additionally, from an interface developer/manufacturer’s perspective, the built-to-print approach carries with it avoidable risks.
Jayco’s Mistry says that the most efficient and effective approach to interface design usually involves a team approach that includes the product engineering staff as well as the interface supplier. The latter would provide consulting and design expertise based on the experience and diversity of interface hardware and software engineers, human factor experts, product designers and manufacturing expertise. This consultative process can reduce product development time and costs while solving complex problems with superior solutions and packaging.

“By working together the team can ensure that all of the relevant ideas are thoroughly explored, and that various manufacturing issues are taken into account,” Mistry says. “I think the best interfaces are simple and intuitive,” he adds. “But that is not easy. What is required is a thorough understanding of the application, an understanding of the environment that the product is going to be used in, and the technologies that are available to achieve the end.”
To complement the consultative approach, Mistry’s firm goes a step further by providing a digital or virtual prototype so that the customer can see precisely the proposed solution as well as how it will fit and operate in the end user’s environment.
Virtual prototyping, which employs the use of CAD and CAE software, enables the interface development expert to both generate and validate a virtual interface design before creating a physical prototype, a capability that can save product manufacturers sizable amounts of time and money.
For example, there is increasingly limited space available for locating an interface on a product. Creating a virtual prototype can ensure that everything can be packaged properly without fit or interference issues, or manufacturing or reliability problems.
Anticipating Challenges
One of the best reasons to consult with an interface specialist before designing the interface is the need to meet several challenges that are “moving targets” as products and application requirements evolve.
For example, ensuring that interface devices, including enclosures and attachments, are ruggedized for environmental conditions should also be a vital concern. In the case of some applications, this includes protection against corrosive environments, providing for ultra-rugged applications that require military-grade shielding, protection against shock or vibration, contaminant sealing, daylight readable, night vision lighting and extended-life grade products.
Also, it is ideal to get a complete interface assembly from a sole supplier, rather than only the interface components. This will help to ensure proper integration, provide plug-and-play connectivity, and save the customer from having to deal with the additional suppliers. For instance, a specialist can supply the entire assembly through to electronic communications from display to host computer, including encryption if required.
This article was submitted on behalf of Jayco mmi, Inc., Corona CA. For more information, visit www.jaycopanels.com.
Subscribe to our FREE magazine,
FREE email newsletters or both!Latest News
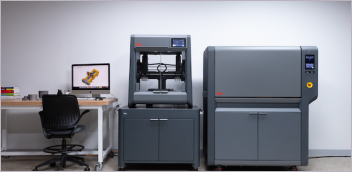
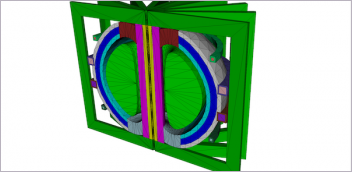
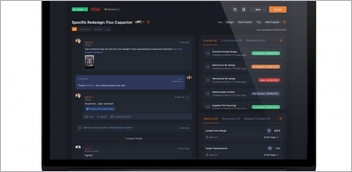
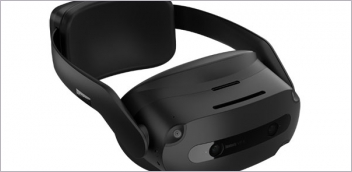