
National Instruments’ NI SOM (System on Module) enables design teams to deploy reliable, complex embedded systems faster because it is based on and has the same rigorous design standards as the LabVIEW reconfigurable I/O (RIO) architecture. Image Courtesy of National Instruments.
Latest News
December 1, 2014

A quick Google search on the Internet of Things (IoT) shows no shortage of stories recounting how the technology is poised to transform everyday practices. From helping doctors facilitate proactive health care to arming service technicians with what they need to administer preventative product maintenance, the IoT also has the chops to alter day-to-day work for engineers, eliminating much of the guesswork that’s become a routine part of the design process.
Next-generation products outfitted with embedded sensors, actuators and other technologies will be able to detect things about their environment—temperature changes, for example, or an imminent part failure—and communicate that information in real time over the standard Internet Protocol to a database accessible by engineers. From there, engineers could analyze this trove of product-related data as part of their regular workflow to guide future product designs, address persistent quality issues, and inject more realism into verification and testing procedures.
While there is huge potential for IoT to close the loop between engineering and how a product is used and performs in the field, the technology to do so is still relatively immature and it’s very early on in the IoT technology adoption cycle, according to Michelle Boucher, vice president of engineering software research at Tech-Clarity, an independent research firm.

“There’s a lot of opportunity for this data to be made available to engineers so they can make better decisions, but it’s more of a visionary thing than actually happening, at this point,” Boucher says. “The ultimate goal is for PLM (product lifecycle management) tools to be able read in the information and mine some of the data with analytics so it’s accessible to engineers when they’re using CAD or simulation tools and when they’re making design decisions.”
The Big Reveal: Customer Usage Patterns
Dassault Systemes sees three primary roles for IoT data as it relates to product design, according to Michael Munsey, the company’s director of semiconductor strategy. Products in the field would collect usage data that could be enlisted to make subsequent design iterations of a car or consumer appliance, ensuring the next generation performs more effectively for the customer. IoT data could also be leveraged to automate processes related to the product that would make its use case more efficient—for example, automating parts replenishment as well as predictive maintenance, Munsey says. Finally, an intelligent product design can minimize the need for human intervention via its ability to automatically adjust based on usage patterns and performance.

For engineers, the possibility of applying such real-time product usage data to the requirements process has significant advantages. Today, the requirements process is mostly manual, starting with a set of marketing and business requirements that get translated into functional specifications for the engineer. The ability to automate the flow of customer-driven usage data directly into a system-level design would give engineers a whole new set of requirements that would help ensure the right product is being developed at the right time, Munsey says.
“Now you have real-time customer use data that didn’t exist before,” he says. “The ability to understand how customers are using the products helps drive new features and functionality that customers need as opposed to trying to guess at what they need.”
This capability would be particularly useful to avoid over-engineering products, a common practice that grossly inflates development costs. “We are already operating in a very complex world where the risk is huge,” says Zvi Feuer, senior vice president and general manager of Manufacturing Engineering at Siemens PLM Software. “Companies take enormous precautions and build a lot of safety nets into products. With this data collected and analyzed in a smart way, you eliminate the need to overcome risk by overdesigning and making products unnecessarily complex.”
Tom Shoemaker, vice president, EPLM segment at PTC, concurs, using an under-utilized air conditioner compressor in a car as a real-world example. “If you can see that something is being used in a certain way—for example, air conditioning is not running as much as initially expected—it becomes clear there is a need for a better system or a cost savings opportunity for OEMs (original equipment manufacturers),” he explains. “After releasing a product, all manufacturers almost immediately create a change request to take 10% of the cost out of the product. They know the product is over-engineered, they just don’t know how. Feeding that information back so it could be used in the next variant of product would be extremely useful.”
The real-time customer usage data collected by IoT devices could also be instrumental to improving test environments and simulation. For example, as opposed to analyzing test and verification data through post-processing analysis, a design team could directly tap into a repository of real-time data, time stamped with the event and sequence information, so they could pinpoint and understand exactly why and under what conditions a particular design failed, says Andy Chang, senior manager for academic research at National Instruments.
And imagine using that same real-time usage data to create the actual test environment as opposed to creating it through higher level modeling. “Using real data gathered by products in the field creates a more robust and comprehensive set of tests,” says Munsey. “The evolution of driving verification and simulation off of real data is a huge advantage because engineers aren’t guessing any more. They aren’t trying to model predictive behavior, but rather are using real data to do the testing and simulation.”

Both the simulation and test use cases converge with another big area where IoT data can lend a hand: Bringing design engineers directly into the loop on how the product is used in the field as part of their on-going quality efforts. “There isn’t currently a closed loop system to what’s happening in the field with products,” says Tech-Clarity’s Boucher. “All the little things that happen as a result of everyday use don’t always get back to the engineers … so they don’t know when something is returned or if there are quality issues.”
Search and Analytics: The Next Big Thing
To ensure the IoT vision has impact for engineers, a number of things need to come together. The data from sensored products and production equipment needs to feed into a common repository that is organized and easily accessible to engineers. Most of the major PLM players, including Siemens PLM Software and Dassault Systemes, see that central repository being PLM, enhanced with new capabilities in the areas of search, for both structured and unstructured data, among other capabilities. Dassault’s acquisition of Exalead, what it dubs information intelligence, and Siemens PLM Software’s buy out of LMS move both companies toward being able to search, explore and analyze vast pools of internal or external, structured or unstructured data.
Yet there are limitations as to how much data you can effectively store in PLM, and requirements for robust analytics and visualization tools that can help engineers make sense of the IoT data and make it actionable for future designs. For example, while PTC’s Windchill Product Analytics, part of its PLM portfolio, lets engineers drill down into compliance, performance and risk indicators on a product structure, it’s not equipped to handle the so-called Big Data arising from IoT devices, Shoemaker says. That is an area that PTC has earmarked for future development, Shoemaker acknowledges, although he declined to provide more specifics.
National Instruments is also working on technology to help engineers make sense of what’s undoubtedly likely to become a deluge of IoT data. For example, the NI System on Module (SOM), the smallest iteration of its embedded hardware, can be deployed much closer to the sensors and actuators on products or industrial test equipment, creating a platform that can help filter the data.
“Now that you can put embedded intelligence closer to the sensors and actuators, it means you can filter out the right signals and pass on only the information that’s relevant to the design,” explains NI’s Chang. “Being able to use the most insightful data for design rather than just collecting all of the data existing on the system is they key.”
What is also likely to be key is the establishment of a new role in engineering—that of data analysis expert, who is knowledgeable of the systems, IoT data and analytics, and who can help deliver information to engineers in a presentable way.
The reality is, in order for the IoT to truly transform the design process, it’s got to be as seamless as possible for engineers to dig in. “If engineers can get access to information without disrupting their workflow it’s going to empower them a lot more,” says Boucher. “Otherwise, it’s just one more thing to take a look at and they’re already under so much pressure.”
More Info
Subscribe to our FREE magazine,
FREE email newsletters or both!Latest News
About the Author

Beth Stackpole is a contributing editor to Digital Engineering. Send e-mail about this article to [email protected].
Follow DE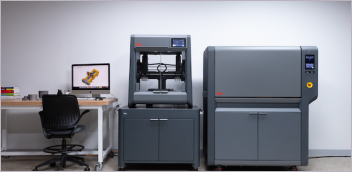
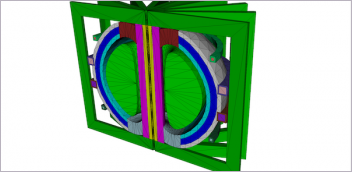
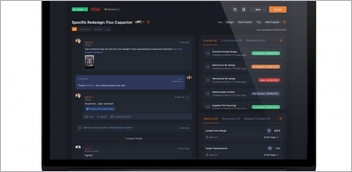
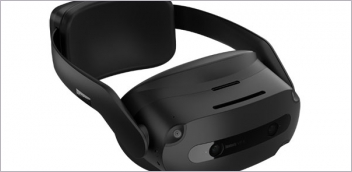