Latest News
March 3, 2008
By Russell Shuba
![]() These images show different views of Abaqus FEA of a Kiekert strength test in a longitudinal direction. The figure at top left shows the complete configuration.The one at top right shows only the latch and striker parts (without test rig). The figure at the bottom left is a cutting plane view through the catch. The small center inset image shows that the catch was pulled out. Finally, the graph at lower rightindicates the reaction-force (in newtons) reached during the test. |
While airbags and seatbelts get all the attention with regard to automobile safety, keeping car doors securely fastened during automobile accidents is another important aspect of occupant safety. Despite a lack of public awareness, developing safe door latches is a high priority for automotive manufacturers.
Imagine designing for German latch maker Kiekert, which has been making automobile locking systems since 1857, owns 500 patents, and was the first to commercialize such innovations as central and power locking. The company produces 35 million door latches every year for Daimler AG, Chrysler, VW-Group, BMW, PSA (Peugeot & Citroen), Renault, Ford-Group, and GM, to name a few.
Your design must meet various government safety standards and satisfy different OEM design specifications in a cost-effective, timely manner. It’s a challenge for anyone, and while Kiekert’s products also include power sliding doors, remote locks, and liftgate and trunk-lid actuators, its core product remains side-door latches.
Hidden Critical Components
The exterior handle and lock cylinder of a car door are connected to a complex inner system of cables, cams, levers, couplings, actuators, gears, pawls, and catches. In this door latch system, there can be 30 parts in a small latch, 75 in a large one. When activated, the catch and pawl secure the door by clamping around the striker, a U-shaped piece of metal bolted to the vehicle’s B-pillar (where the seatbelt is also fixed).
The side door latch enables a multitude of door functions such as opening and closing from inside or out, locking and unlocking from inside or out, central-, childproof-, and remote-locking, and more. And the entire system must continue to function for years at a wide range of temperatures, within specific noise and vibration limits, and must be strong enough to survive a crash. The integrity of the latch-striker connection is critical to that strength.
![]() Abaqus 3D FEA meshed model of a car door striker- latch interaction under maximum force (up to 3 metric tons) at end of a strength-test run.This test is on the latch in the primary position — when the door is completely closed. Strength tests on the secondary position (when the door is secured but not fully closed) are applied using lower forces. In this image, the latch can be seen clamped through the loop of the U-shaped striker, holding fast despite deformation of catch, pawl, and B-pillar plate. Greyareas indicate highest strain. |
“Strength testing of door latches is fundamental for us,” says Thomas Waldmann, manager of the Technical Analysis and Simulation department at Kiekert. “Not only do we have to meet standards set by governments (the Economic Commission for Europe and the U.S. Federal Motor Vehicle Safety Standard), but each car manufacturer has its own testing requirements as well.”
Waldmann heads a global group that focuses on computer modeling of door-latch components with primary emphasis on full virtual validation. The design simulation planning and report (DSP&R) validation program was developed over many years and includes more than 80 different simulations and calculations.
“Kiekert’s engineering tools provide a high quality level of results,” says Waldmann. “Our unique body of knowledge and our testing database ensure low project risks and the most efficient design process in the latch industry.” Meeting global standards for strength testing (currently about 1.1 metric tons — 11,000 newtons (N) — of force applied to the latch-striker connection from multiple directions) is relatively easy, says Waldmann. The real work is meeting the expectations of Kiekert’s OEM customers. “Most customers’ standards are about twice their government figures.
Quality, Quickly
“We start with CAD models from the design department and run them through a three-part process that includes finite-element modeling, multi-body dynamic simulations, and tolerancing,” says Waldmann. “All of which must be done accurately in the least amount of time.”
Since it began using the virtual validation process, Kiekert has significantly reduced the number of tests for product design validation. “Our time to market for a new latch is now less than 18 months,” says Waldmann.
Unified FEA for Complex Analysis
The key to speeding up latch design and development at Kiekert has been the addition of Abaqus software from SIMULIA, Dassault Systemes’ brand for realistic simulation. “Physical testing in a laboratory is slow and can’t realize the whole job,” says Waldmann. “We began our linear computer modeling of door latches with finite-element calculations inside CATIA V4 ELFINI. Adding Abaqus enabled us to do more complex nonlinear simulation, which is what we need for accurate strength testing in three dimensions.”
Abaqus unified FEA works well with Kiekert’s existing design software. “We can mesh complex parts in CATIA V4 and V5 and then export the meshes to Abaqus,” says Waldmann. “We use Abaqus for CATIA, in conjunction with Abaqus/Standard, Abaqus/Explicit, and Abaqus/CAE. We never have any problems getting what we want because we have different ways to get our solutions.” Using the implicit and explicit solvers in Abaqus to solve the right type of problem is easy, Waldmann points out. “And modeling the nonlinearity of contact is something Abaqus does best.”
Choosing the elements for meshing the lock design is often task-dependent, Waldmann notes. Automatic meshing is a must in order to build models efficiently for Kiekert’s complex latch assemblies. “The advantage of using tetrahedron elements is that it takes only half an hour for meshing. We need a little bit more CPU time for the job because we are modeling many small parts, but we save time with the meshing.”
For modeling riveted connections, Kiekert fully models its own rivets for the finite element analysis. “We need to control the stress distribution in the rivets, which is essential for latch strength-test calculations,” says Waldmann.
Waldmann’s group has a 16-CPU cluster and primarily uses a Linux operating system. Most Abaqus jobs at Kiekert are run on four CPUs, providing substantial simulation throughput and efficiency. “We can run up to four jobs at once, usually overnight,” he says. His team can also use Unix platforms for calculation, or PCs with Microsoft Windows for Abaqus CAE. An average job has between 700,000 and 1.5 million degrees of freedom.
![]() An actual photograph of a Kiekert latch module is shown after strength testing. |
Plastics vs. Steel and Other Tradeoffs
Materials selection is important when modeling a virtual door latch. The first latches built were made entirely from steel or aluminum alloy. But today, multifunctional latches include plastic parts, even electrical motors, added for ease of function, noise reduction, or comfort.
Kiekert has established a unique material database over the years. “Accurate material data is the basis of exact simulation results,” says Waldmann. “Kiekert has invested significant time and money in running scientific material tests to generate that data.”
Using the Change Material function in Abaqus, Kiekert can evaluate plastics ranging from zero to 50 percent glass fiber content. But parts designed for safety must remain steel, Waldmann says, not only for strength but for fire-resistance. “We have a long history working with different grades of steel with special heat-treatment capabilities. We search for the best balance between flexibility, strength, and abrasion. With the Change Material function we can put a part through various stresses and see what works best. Sometimes we run the same job with the same geometry with five material variations.”
Compliance with a world standard In an effort to reduce those numbers, the U.S., the European Union, Canada, and Japan have adopted the first global technical regulation (GTR) for motor vehicles to set minimum safety standards for door locks and retention components. Each country is aligning its domestic regulations with the world standard: voluntary compliance is in effect now in the U.S., becoming mandatory in September 2009, according to the NHTSA. Most existing U.S. standards were established in the early 1970s. |
Kiekert also uses FEA for evaluating temperature and noise-vibration, says Waldmann. “The parts of a latch, particularly the plastic ones, must continue to work between -40 and 85 degrees C (-40 to 185 degrees F). As for the noise-testing department, they want more plastic to reduce noise whereas I want more steel for strength. We always need to satisfy both noise and safety considerations, but using Abaqus makes it easier to adjust your design and test the results.”
Putting on the Pressure
When it comes to virtual strength testing, Waldmann’s department comes down hard on its latch designs, loading two to three tons of virtual force (20,000N-30,000N) on the connection between latch and striker. All manufacturers require that strength tests are carried out along both longitudinal and transverse planes; sometimes vertical and transverse plus 45-degree rotation tests are included (rotational testing was a recent request from an OEM in the U.S.).
FEA testing provides a safer way to evaluate latches than pulling apart real steel parts in a laboratory. “When we do virtual loading with FEA, we can make cutting planes during testing to look inside and see exactly what happened without the danger of steel shattering during physical testing,” points out Waldmann. Using FEA, Kiekert engineers can also evaluate the sequence of events more incrementally, as stresses are applied to a latch, and observe internal structural changes that may not be reflected in the appearance of an actual latch at the end of reality testing.
Mass-scaling Cuts Processing Time
Kiekert performs both its finite element analysis (and its government regulation testing) on latches on a quasi-static basis (at a rate of 5 mm per 60 seconds). To cut FEA processing time, Waldmann uses the mass-scaling function in Abaqus Explicit, which allows him to reduce total computational time by increasing the stable-time increment.
“A huge number of calculations take place in an explicit code, which can result in a longer run time,” he says. “Mass scaling is the answer, but you have to get a feel for how to do it with quasi-static calculations: If you see the door striker start jumping too much, you reduce the stable-time increment further.”
Waldmann’s group uses the results of its FEA testing to recommend design changes that improve the performance of the latch. “We can change the geometry, which saves material costs, or we can change the material itself,” he says. “We can also add more parts, but we try to avoid that approach, which is the most expensive. Whatever material we are testing, we are looking for the best for strength and cost.”
Real Crash Data in the Future?
Since a latch is part of an entire door locking system containing handles, cables, rods, etc., developing a theoretical forecast of the complete latch system behavior during a crash will be the next step in increasing car-door safety. “Kiekert has begun designing an integrated latch module in a holistic approach to optimize such door-locking system behavior,” says Waldmann.
A real car crash takes only milliseconds, he notes. “Currently, OEMs calculate their car simulations with just a single element showing that the door is closed. I’d like to ask them to measure actual crash data from the location in the door where a latch would be and then give us those results. Then we can model parts of the door and the B-pillar and calculate the latch within them to make it stronger in a real crash.”
For now, Waldmann’s group has reached the point where the FEA and other simulation tools they are using have enabled them to make the most realistic calculations in the latch industry. Such state-of-the-art simulation capabilities are one of five Kiekert selling points (the others are innovation, complexity management, experience, and product validation) that have made Kiekert the top latch supplier worldwide, according to Waldmann. “We spend a lot of time adjusting the geometry of our latches for the best result,” says Waldmann. “The simulation department is an essential part of the Kiekert design process.”
More Info:
Kiekert
Heiligenhaus, Germany
kiekert.de
National Highway Traffic Safety Administration (NHTSA)
Washington, DC
nhtsa.dot.gov
Abaqus
SIMULIA
Providence, RI
simulia.com
Russell Shuba is a freelance writer who lives outside Madison, WI. When he’snot tracking down the details of his latest assignment, he can be found plyingthe north country’s lakes in a homemade kayak or skiing in the backcountry.To comment on this article, please send an e-mail addressed to [email protected].
Subscribe to our FREE magazine,
FREE email newsletters or both!Latest News
About the Author

DE’s editors contribute news and new product announcements to Digital Engineering.
Press releases may be sent to them via [email protected].
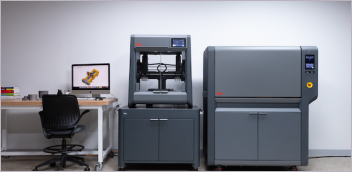
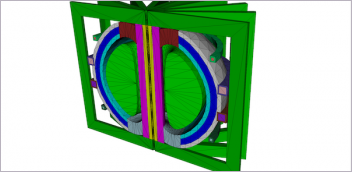
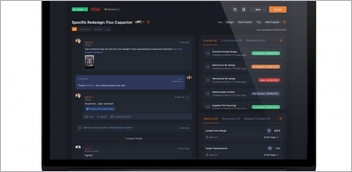
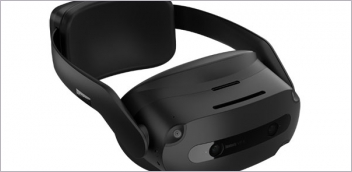