Lofty Goals Demand Precise Positioning
SpaceX looks to accomplish tasks that are literally out of this world.
Latest News
September 1, 2011
By DE Editors
With the retrieval of Dragon from the Pacific Ocean, Space Exploration Technologies (SpaceX) became the first commercial company to launch and recover a spacecraft from Earth orbit. Placed into space atop the company’s Falcon 9 launch vehicle, Dragon completed two orbits with speeds topping 17,000 miles per hour. After its three-hour, 50,000-mile flight, Dragon splashed down at the predicted time.
This was the first flight under NASA’s Commercial Orbital Transportation Services (COTS) program, designed for companies to demonstrate International Space Station (ISS) resupply capabilities. Following completion of COTS missions, Dragon will begin regular flights to the ISS. For these missions, SpaceX will again turn to its portable coordinate measurement machine (PCMM) systems to maintain the precision it achieved when first launching and returning Dragon from orbit.
![]() Falcon 9 lifts off from SLC-40 for the first test flight of Dragon Spacecraft. |
SpaceX is a different kind of company, thanks in part to its founder, CEO & CTO Elon Musk, who was co-founder of PayPal and is the CEO of Tesla Motors.
In a post-flight press conference, Musk said, “The reason I’m doing SpaceX is that I just happen to have a very strong passion for space, and I want us to become a true spacefaring civilization, and even a multi-planetary civilization. That is my goal for SpaceX.”
To make his goal a reality, SpaceX is changing 40-year-old paradigms with a family of launch vehicles and spacecraft that increase reliability and performance while reducing costs “ultimately by a factor of 10. The underlying philosophy is a focus on simplicity to both increase reliability and lower cost for vehicle development and launch services.
According to Larry Mosse, SpaceX’s tooling operations manager, the company counts on its PCMMs to help deliver this reliability and cost reduction. And it counts on Verisurf metrology software to drive all these devices in a powerful, yet simple way.
“Verisurf metrology software is doing its part in maintaining precision in the shop and on the launch pad,” says Mosse. “We use it for everything from tooling fabrication to pre-launch preparation.”
Ground Control
Falcon 9 lifted off from Cape Canaveral AFS launch pad SLC-40 at 10:43 a.m. EST on Dec. 8, 2010. At 10:46 a.m., the first stage separated. At 10:52 a.m., Dragon entered Earth orbit. At 2 p.m., Dragon splashed down in the Pacific Ocean.
According to the company, Falcon 9 delivered Dragon to orbit with “near bull’s-eye insertion,” and Dragon then splashed down safely into its targeted landing zone.
The accuracy of the flight path required careful alignment of Falcon 9’s sections and precise launch vector positioning. The SpaceX crew used its PCMM metrology systems, which included Leica trackers and Verisurf software.
SpaceX founder, CTO and CEO Elon Musk stands with Falcon 9 at Cape
Canaveral AFS.
Falcon 9 is 157 ft. tall with the Dragon spacecraft, and has a 12-ft. diameter. Nine of SpaceX’s Merlin engines power the first stage; the second stage uses a single Merlin Vacuum engine. Final assembly of this piece of engineering is completed at the launch site.
To position and align Falcon 9’s components, SpaceX used Leica laser trackers and Verisurf’s BUILD application, which is a virtual gauge. The trackers fed measurement data directly to Verisurf, which reported, in real time, the accuracy of each section relative to the CAD model used in design and manufacturing.
After assembly, the SpaceX crew raised Falcon 9 into its vertical launch position. To follow its intended flight path, launch specifications allowed the vector of the vehicle to deviate by only 0.02 ° over the 157-ft. length. Mosse says that they again turned to the PCMMs to confirm a “ready-to-launch” status.
“The specs allowed the nose to be off of vertical by 6 in.,” he explains. “Verisurf reported that we had only a one-hundredth’s-inch deviation East to West, and three-hundredths from North to South “and from the ground up, all sections were at their nominal positions.”
Mosse notes that this alignment accuracy was possible because of the controls used in manufacturing and assembly operations at the company’s Hawthorne, CA, facility.
“We have a set of five fixtures that are used to position rocket components and drill a pattern of 144 holes,” he offers as an example. “These holes dictate the alignment of Falcon 9’s sections.”
As he did in pre-flight preparation, Mosse used Verisurf to place the fixtures before committing to the drilling operations.
“With Verisurf, we are looking directly at the CAD model and the measurement results,” Mosse states. “We see the measurements reflected against the 3D model. This makes the process faster and reduces mistakes.”
Rendering of Dragon orbiting with solar panels extended.
He notes that before Verisurf, his team had to interpret page after page of 2D drawing dimensions.
“We had to rely on people’s ability to visualize 3D measurements from 2D drawings, which results in interpretation problems,” he says.
Before assembly, Mosse used his PCMMs to measure parts and tooling during fabrication and manufacturing. For example, SpaceX will drive both Leica trackers and Romer arms with Verisurf when measuring composite tooling or weld fixtures.
“We inspect these items to the CAD data. In many cases, we will inspect to profile tolerances only,” Mosse says. “We aren’t drawing free, yet, but like the rest of the aerospace industry, we are striving to implement model-based definition to achieve its many benefits.”
For SpaceX, the most important benefit is time. Model-based definitions with profile tolerances eliminate the time to document an engineering drawing; reduce the time to create inspection plans and reports; and accelerate identification and resolution of manufacturing issues. With an aggressive schedule of more than 30 Falcon 9 launches over the next four years, including 12 space station deliveries, every moment counts.
SpaceX’s philosophy is that through simplicity, it can deliver more reliable vehicles at a lower cost. SpaceX counts on Verisurf to help deliver on this goal.
“With Verisurf, we have very quick assurance that we are in the proper 3D space,” Mosse says.
For More Information:
This article was contributed by Verisurf.
Subscribe to our FREE magazine,
FREE email newsletters or both!Latest News
About the Author

DE’s editors contribute news and new product announcements to Digital Engineering.
Press releases may be sent to them via [email protected].
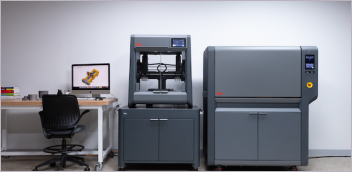
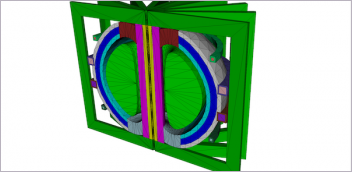
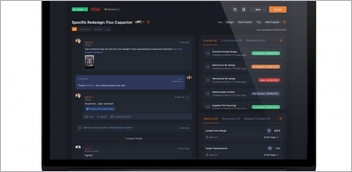
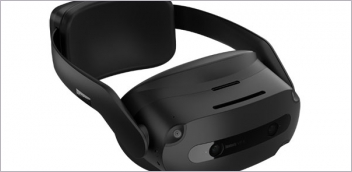