Latest News
February 21, 2008
By Susan Smith
Autodesk World Press Day 2008, held at the Intercontinental Mark Hopkins in San Francisco February 12th and 13th, attracted technology industry press from all over the world to learn about Autodesk’s upcoming product releases and the challenges facing designers and engineers in today’s world.
CEO Carl Bass opened the General Session on Tuesday by addressing those challenges.
Autodesk successes include 9 million users of Autodesk worldwide (registered users); 98 percent of the Fortune 500 companies use Autodesk products; Autodesk celebrates 25 years of financial success; the company’s net revenue is expected to exceed $2 billion this year; cash and equivalents exceed $800 million; and no debt.
![]() Autodesk CEO Carl Bass |
Bass spoke of a new “convergence of technology across multiple disciplines,” describing how we are already seeing products such as the freeform design tool — Autodesk Maya — used in manufacturing, and now it is being marketed to architectural users as well. In addition, Autodesk Inventor solid modeling software for parametric rules-based design is moving away from a strictly manufacturing role to adoption by the architectural, engineering, and construction industry.
Bass cited big macroeconomic trends driving product development:
Digital life— Everything has gone from analog to digital: the way we communicate, and entertain, according to Bass. Bass pointed to the image of kids listening to an iPod while talking on the cell phone, and that this may be a way of creating information. On YouTube, 100 million videos are downloaded every day, and there are 65,000 new videos uploaded every day.
“The largest analog collection of data is probably in the Library of Congress,” said Bass. “Google has already indexed about 1,000 terabytes of data per day - 100,000 times more than what’s in the Library of Congress.”
Obviously, how people gather their information has changed, and now the way we educate children and train a workforce change to keep up with this process.
Bass looks to the entertainment industry, which has always been a leader in the use of new animation and video technology. The entertainment industry has always tracked things like quality and emotional content that we generally don’t associate with architectural or engineering or even automotive design, although it has always been there. These are subtleties that the designer knows firsthand, but does not always put into words.
Globalization — The digital life is a large driver of the next big trend — globalization. New business models need to be explored to deal with the growing commoditization, cultural change and slackening of trade rules.
The Infrastructure boom is driven by the first two trends. There is a boom to rebuild, build and repair the world’s infrastructure. Over the next decade, China plans to build over 30 new airports. Aging infrastructure needs to be rebuilt or replaced all over the world. An aging workforce also adds to the urgency by creating a need to educate a younger workforce quickly and impart a valuable knowledge base.
Global Climate Change — The rising cost of energy coupled with the rising use of energy result in a need to find better ways to produce energy and get smarter about consuming it.
Buildings are huge consumers of electricity and natural resources, but with more effective designs we can be producing zero carbon footprint buildings.
Bass said almost jokingly that the thing that spurs most invention is making mistakes, so it’s important to have tools to allow you make more mistakes less expensively.
Manufacturing News
What must manufacturers address to be best-in-class? The answer to Autodesk general manager of Automotive Ed Martin’s question was as follows:
- Innovation — 75% of executives considers innovation most important.
- Globalization — The spread of capital, labor and knowledge around the world.
- Sustainability — Manufacturers need to address sustainability in many ways, for example: manufacturing, operation and disposal.
Digital prototyping is changing the manufacturing market, according to Martin. 3D by itself doesn’t accelerate innovation. Digital prototyping leverages the power of the 3D model. “It’s about starting digitally from the first concept design, to evaluate how different subsystems react. It provides tools for simulation and analysis,” Martin said.
Martin noted that by combining BIM and digital prototyping we can design a more sustainable system. Product launches can be accelerated using digital prototyping, and can connect industrial design and engineering.
In the automotive industry, Class A surfacing can be brought closer to concept design, and the Class A process can be connected to the engineering process.
Martin also addressed the transportation industry in general. “Volumes are typically lower in transportation, the cost per vehicle is higher, and there is much more customization involved. Mechanical and electrical processes that are used in transportation must be integrated.”
In discussing industry workflows, Martin pointed out that the consumer products industry considers function and aesthetics as a critical part of design. 3ds Max and Maya design tools are being used to produce promotional material. The automotive industry uses Inventor, Alias Studio and Showcase, as well as Revit. Among the features of Inventor 2009 is the native 64-bit support, which is very powerful for creating industrial machinery. The release also has cable and harness enhancements integrating electrical and mechanical systems design used in transportation.
Jeff Richlin, president, Richlin Machinery, spoke of that company’s transition to automation, going from using 2D Visio drawings to Inventor. The company builds custom machine tools and precision machinery such as small CNC lathes. Once they got Inventor they used reverse engineering to put effective systems in place quickly.
“Inventor changed our world,” declared Richlin. Besides using it to create their designs, the company can use Inventor to translate ideas to customers and the marketing department, pull information from their legacy systems and paste into their new designs, and use this information for providing quotes on jobs and materials.
Richlin is also using animation for communication. They also use Vault and Productstream, and AutoCAD Electrical for PLC programming. “Vault allows us to go backwards after we make mistakes,” said Richlin. This works well as they don’t have a lot of engineers on staff.”
Some of the key enhancements in the 2009 release of Inventor include easy to use simulation tools integrated within the product, NavisWorks for multidisciplinary design review, and Productstream publishing to Microsoft SharePoint. Altogether there are more than 650 enhancements in the entire manufacturing suite of products for digital prototyping, according to Autodesk Manufacturing Industry manager Keith Perrin.
Customer: Ford Motor Company
Peter Horbury, executive director of design for the Ford Motor Company, said that more tools such as Maya and 3D Studio Paint are becoming part of the design process for auto manufacturers.
Horbury also stated that there are three components for expediting the design process –people, working digitally and process.
Focusing on the people at Ford Motor Company, Horbury credited their designers with being very good at converting clay models into 3D sculptures. “Those guys know 3D and we give them a new tool to do it quicker,” said Horbury.
Technology is “all about hardware and software, and we have invested millions in new equipment,” Horbury said. “It’s all about globalization. We have design studios in America, China, Australia, Europe, and have an entire studio in Detroit dedicated to R&D.”
Ford Studios are now completely digital and can optimize the workflow and processes of design. According to Horbury, Ford owes much of its design success to its digital capability. “Our time to market is 14 months faster than it was a year ago using the tools.” In addition, Ford has experienced a dramatic reduction in physical prototypes, and they can make a prototype available years ahead of production.
Paint and colors and RT RT (real time ray trace) are utilized to accurately calculate virtual paint characteristics in varying light conditions. “You can actually show dealers what the truck will look like in their own dealership,” said Horbury.
The combination of 3D visualization software, a 3D model and a milling machine can turn a screen image into a full sized vehicle overnight. The mill is accurate to within 4 microns (25 microns = 0.001 thousandths on an inch.)
“Everyone in teams have the same data,” said Horbury. “It used to take 7 weeks to take from rendering to a model, now it takes only 2 weeks.”
Subscribe to our FREE magazine,
FREE email newsletters or both!Latest News
About the Author

DE’s editors contribute news and new product announcements to Digital Engineering.
Press releases may be sent to them via [email protected].
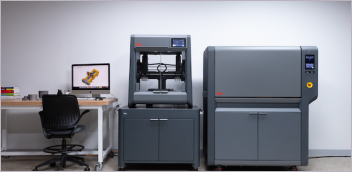
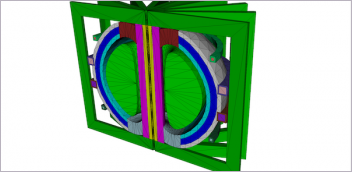
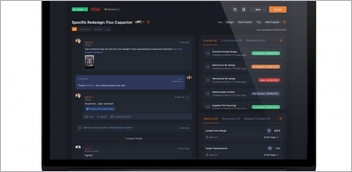
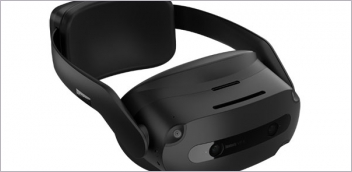