
Latest News
July 1, 2014
By Bernie Rosenthal
The regulatory landscape for automobile emissions continues to evolve. In February, the European Commission endorsed new, substantially lower target emissions for carbon dioxide (CO2) emissions from motor vehicles. In March, the U.S. Environmental Protection Agency (EPA) also announced new, tighter fuel emissions standards to help curb greenhouse gas emissions.
For today’s engine and automobile manufacturers, designing engines that meet mandates for cleaner fuel standards is a growing challenge. While regulatory agencies require cleaner burning engines, the market demands more powerful motor vehicles with improved fuel economy. To streamline the design of high-efficiency, low-emissions engines, computational fluid dynamics (CFD) simulations allow engine designers to visualize and test fuel and ignition behaviors within a virtual combustion chamber, using software instead of costly physical prototyping. Virtual prototyping using CFD gives engine manufacturers a faster way to design cleaner, more efficient engines by simulating ignition and fuel dynamics.
To ensure that simulations can accurately predict real-life pollutant emissions from internal combustion engines requires CFD simulation tools that accurately account for chemical kinetics. Combustion performance is one of the key areas of design optimization in the automotive development process, and at the heart of combustion is chemistry. Understanding and accurately predicting the effects of fuel chemistry in a combustion system is critical to developing competitive real-world engines with superior performance and lower emissions.
Improving Simulation Accuracy
Motor fuels are very complex. Not only do they vary by seasonal formulation (for instance, in the U.S. summer-grade gasoline contains less butane than winter formulations), fuels differ by region: Diesel fuel used in the U.S. has different properties than diesel fuel used in Europe. In addition to fuels composed of hydrocarbons, there are non-carbon-based alternative fuels such as ethanol and bio-diesel. To add to the complexity, certain chemical species in fuels contribute more to emissions than others, underlining the need for multi-component, chemically precise fuel models for accurate modeling.
To improve the predictive accuracy of combustion simulation, the Model Fuels Consortium, a 20-member group that included leaders in energy and engine manufacturing, pioneered the use of “surrogate modeling.” With this process, complex fuel chemistry could be represented by a reduced number of well-characterized molecular models and reactions selected to accurately simulate specific behaviors such as pollutant-emission production. The consortium, which included Toyota, GM and Volkswagen, among other global automakers, identified 56 fully validated fuel components comprised of more than 4,000 chemical species. These findings were compiled in the Model Fuels Library, a database of detailed chemical mechanisms for use in combustion simulations.
Getting to the Root of Soot
Soot emissions are particularly difficult to predict with conventional CFD simulations. Soot formation involves multiple complex chemical interactions combined with physical interactions that take place in an engine. Engine operating conditions such as combustion pressure, temperature, fuel‐air equivalence ratio, quantity of exhaust gas recirculation (EGR), and boost level can all affect the formation of soot. And once a soot particle is formed, it can grow and combine with other soot particles through agglomeration, or it can oxidize. Because of the many factors that can combine to give rise to soot, it is difficult to represent with simple modeling tools and single-component, severely reduced fuel models used in most conventional CFD packages.
To ensure that simulations can accurately predict real-life fuel effects requires more than just the use of complex algorithms to describe the physics and thermodynamic behavior of combustion; they also require a detailed understanding of fuel chemistry.
The FORTÉ CFD Package by Reaction Design, now part of ANSYS, provides engine designers with tools to create CFD combustion simulations. Fuel components derived from the Model Fuel Library help simulate combustion for a variety of new or existing fuel blends, and foresee what emissions will occur for a wide range of operating conditions. Multi-component fuel surrogate models also help predict where and when soot will form in the combustion chamber under varying factors.
By using accurate fuel models based on precise chemistry, engineers can increase the predictive quality of combustion simulations—helping them more quickly and effectively meet strict regulatory guidelines, and create advanced clean engine and fuel technologies.
Rosenthal is general manager of Reaction Design for ANSYS. Send e-mail about this article to DE-Editorsmailto:[email protected].
Subscribe to our FREE magazine,
FREE email newsletters or both!Latest News
Related Topics
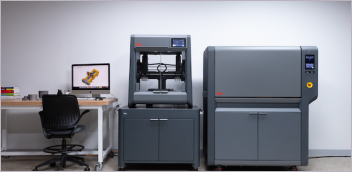
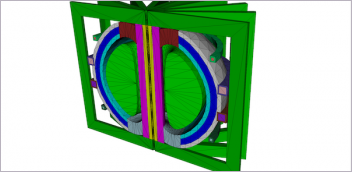
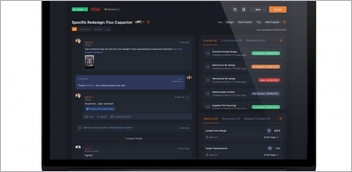
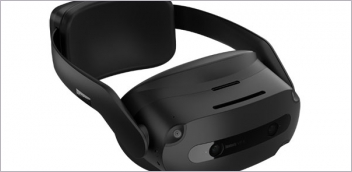