Latest News
February 1, 2011
By Michelle Boucher
The reality for today’s product development is that very rarely is an entire product designed in only one CAD system. The challenge is bringing together all those CAD models, without losing or recreating work. There simply is no time to waste on fixing imported geometry or recreating work someone else has done.
![]() The top two pressures driving the need for multi-CAD. |
A new study by the Aberdeen Group, Working with Multi-CAD? Overcome the Engineering Bottleneck, explores how companies can work most effectively with multi-CAD data.
Study Findings at a Glance The full Aberdeen study is available online at no cost until Feb. 28, 2011. |
Why the Need for Multi-CAD?
In the study, 82% of respondents report using three or more CAD formats in their design process. Even more surprising, 42% report using five or more. The graph below shows the top pressures driving the need to work with multiple CAD formats.
There are a variety of reasons companies must work with multiple types of CAD data—No. 1 being that product development is not done in isolation. A variety of suppliers, external partners and even customers are all involved.
To collaborate on designs, the CAD data must be shared. And because every company is not necessarily using the same CAD product, a multi-CAD environment is created.
The Obstacles of a Multi-CAD Environment
The biggest problem in working with multi-CAD data is that it is not as easy to work with as native CAD. Traditionally, translated geometry behaves as a “dumb” block. So, when engineering change orders (ECOs) come through, manipulating the geometry is very difficult. Often, the easiest thing is to just recreate the geometry, losing any of the time-saving benefits of working from the third-party CAD data in the first place.
![]() The top challenges of working with multi-CAD data. |
Although new CAD technologies have come a long way, CAD data does not always translate cleanly. Engineers are often left with the time-consuming, tedious task of cleaning up the geometry to create a solid model. This process may introduce errors, which result in downstream quality problems.
![]() Table 1: The top downstream deliverables using CAD models. |
Finally, when collaborating with third parties and sharing CAD data, as each party makes changes to the design, it is easy for files to get out of synch. Consequently, lack of revision control means risking that work will be done on an outdated version of the CAD model. This results in subsequent errors because of conflicting information from two different versions, which ultimately hurts product quality.
The Downstream Impact
As 3D CAD has become the predominant design tool and CAD technology has advanced, CAD models have become very sophisticated. In fact, as the chart above indicates, losing the intelligence embedded within the native CAD file is the top challenge. One of the reasons why is that CAD files are now used for so much more. See Table 1.
While it is not too surprising that CAD files are used to produce manufacturing information such as assembly instructions and numerical control tool paths, other uses show that CAD has become important to multiple departments. Sales, marketing, documentation and field service all rely on that digital model—and the information embedded in it—to support them in their jobs. With so many departments relying on the digital model, it becomes even more important to be able to work with multi-CAD data.
Best Practices
To understand successful approaches for working with multi-CAD data, Aberdeen benchmarked the performance of study participants and categorized them as Best-in-Class (top 20%), Industry Average (mid 50%), or Laggard (bottom 30%).
![]() Table 2: Advantages of a best-in-class multi-CAD environment. |
The top pressure creating a need for multi-CAD environments is collaboration. A successful multi-CAD environment is one that addresses the need for it, while simultaneously addressing the top challenges. Four key performance measures that indicate success with this were used to distinguish the Best-in-Class from Industry Average and Laggard organizations (see Table 2).
The Best-in-Class are able to leverage work already done by suppliers and partners, or work from customer specifications to save time in their development process. This improves collaboration and allows them to be more efficient. As a result, they reduce their development time by 32%.
In addition, the Best-in-Class release 90% of their designs on time. Showing evidence of their ability to reuse existing CAD data, they are able to reduce development costs by 31%.
Finally, the Best-in-Class do a better job avoiding problems from CAD data translation or poor version control. This is reflected in their ability to meet quality targets when the design is scheduled to be released 90% of the time.
In addition to being more efficient, lowering development costs and achieving higher quality, the Best-in-Class enjoy other benefits, too. Since implementing their current CAD environment, the Best-in-Class participants have been able to reduce the time it takes to translate CAD data by 24%. This contributes to their ability to reduce development time. Their ability to meet quality targets is reflected in a 25% decrease in the number of change orders after design release. They have also done such a good job addressing the challenge of losing the intelligence in the CAD file that they have been able to reduce the time required to implement an ECO by 26%.
The Best-in-Class are 35% more likely than their competitors to standardize on one CAD application. By standardizing on one application, engineers are more efficient because they can perfect their skills in that one application.
In addition, distributing workloads is not limited by CAD skills needed for specific projects. This makes things easier from a management perspective, as there is more flexibility.
Finally, IT support is simpler because there is only one CAD application to support.
When suppliers and customers use a different CAD tool, the Best-in-Class ensure they can deliver and receive files in many formats, even though they only design in one. They are 29% more likely than their competitors to take this approach. As a result, they can focus supplier selection on part quality and cost, rather than their preferred CAD.
One unusual finding from the study is that delivering or receiving CAD files in neutral formats such as IGES or STEP, while still done, is no longer the preferred practice. The Best-in-Class, especially, are more likely to take another approach. This is a shift from Aberdeen’s findings in the December 2006 Multi-CAD Design Chain Benchmark Report. In 2006, 52% of companies reported delivering designs in neutral formats. This means that, with the advances in available CAD and visualization tools, companies have found better approaches to delivering and receiving CAD data in many formats.
More Info:
Aberdeen Group
Michelle Boucher is a research analyst in the Product Innovation and Engineering practice at Aberdeen Group, where she focuses on identifying product development best practices. She has published more than 50 studies on the use of CAD, CAE, PLM and other topics, including manufacturing planning, systems engineering and mass customization.
Subscribe to our FREE magazine,
FREE email newsletters or both!Latest News
About the Author

DE’s editors contribute news and new product announcements to Digital Engineering.
Press releases may be sent to them via [email protected].
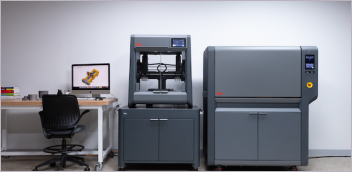
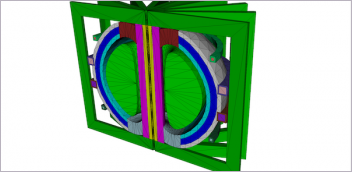
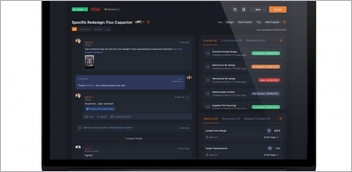
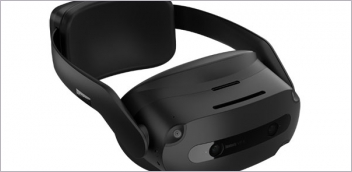