When Safety and Savings Matter
Latest News
May 1, 2005
Laser-scanning reduced reverse engineering costs on a lacrosse goggle project by 70 percent.
By Kevin Vititoe
Reverse engineering plays a significant role at Priority Designs of Columbus, OH, because we are often assigned the task of taking old products and making them function better or meet the needs of a new application. And we do this for customers who make everything from sporting goods to plumbing wares.
Getting a Head Start
One recent example was a project for a manufacturer of protective eyewear for lacrosse players. Priority Designs took on the job of designing the new eyewear last year and was faced with the challenge of reverse engineering a headform model that was provided by the client. The model was based on the target market for which the eyewear would be manufactured.
This project was somewhat different than many taken on by Priority Designs by virtue of the fact that we started with a headform that would be used later to evaluate the effectiveness of the goggles. The client tested its designs by placing them on the headform and shooting a ball at the goggles at a speed of 60 miles per hour. The test is videotaped and analyzed in slow motion to see how the goggles perform. We decided to design the goggles around the headform because it would ensure the right fit for the target market and help the product pass the safety test.
The challenge was in reproducing the shape of the headform. Its many contours represent a very complex 3D geometry that makes physical measurements very difficult to accomplish with accuracy.
Cost of Manual Measurements
In the past, we would have cut the headform into sections, traced the sections on paper, measured each section, entered them into a CAD system, and then used them as the framework to create a surface model. The problem was that it would have taken two or three days to cut the headform and perform the measurements, and another two or three days to input the data into the CAD system. The whole process would have represented at least a week’s worth of work, requiring us to charge as much as $5,000 to the client.
On top of the cost, it would have been difficult to accurately measure the sections; a variable that would depend entirely upon the ability of the technician and the measuring tools used. It would be easy to make a mistake that could cause errors of up to a quarter of an inch.
Another alternative to be considered was a coordinate measuring machine (CMM), but it would not have provided much improvement. It might have eliminated the need to cut the headform into sections and measured the individual points to a higher level of accuracy than hand measurements. But the problem with this approach remains that the CMM captures points individually, and it would have taken us a great deal of time to capture enough points to accurately define the complex contours of the headform, again transferring cost on to the client.
Another Alternative
So we considered laser scanning, which can be used to convert any physical part into a 3D model quickly and with a high level of accuracy. We also recognized that the technology offered a potential for substantial improvements in cost. Laser scanners are able to quickly measure large parts while generating far greater numbers of data points than CMMs, and all without the need for templates or fixtures.
![]() |
This scan of the client’s headform shows the level of detail available using laser scanning technology used by Nvision. |
To record the shape of a component, the technician simply holds the laser sensor so that a line of laser light appears on the part. The laser sensor is moved freely about the object, allowing the technician to capture data in much the same motion as spray painting. As the technician moves the sensor over the surface of the object, real-time rendering of the data on-screen gives immediate feedback. This is important because it lets the technician see areas that were missed so he or she can fill them in with another pass. The system combines the coordinate data with the Cartesian and angular coordinates generated at each position of the mechanical arm. The result is a dense cloud of 3D data describing the surface of the object.
The key advantage of the laser scanner is that it generates far more data points in less time than other techniques. Depending on the size of the part and level of accuracy required, the company typically captures tens of millions of points for each part. And since it’s a noncontact scanning process, the operator does not have any effect on measurements because it is simply a beam of light passing over the object.
Service Bureaus Can Do th Job at a Fraction of the Cost
It wasn’t possible to justify the purchase of a laser scanner either for this project alone, nor for the half dozen or so reverse-engineering projects that Priority Designs performs in a typical year. We were also concerned about the potential for technology changes in laser scanning that might make a recently purchased system obsolete before the company had the chance to earn a payback on the machine. And, we wondered about the justification of passing along the costs of maintaining capital equipment to clients who are accustomed to paying for time and materials only.
![]() |
This accurate solid model of a client’s headform was turned around to Priority Designs two days after it was overnighted to NVision. |
So, we looked into service bureaus and heard about a laser scanning service offered by NVision Incorporated of Southlake, TX. NVision said they could provide a surface model with millions of data points to an accuracy of only a couple thousandths of an inch at a cost that was a fraction of what it would cost to do internally. I shipped the headform to them by overnight delivery, they scanned it in a day with their ModelMaker laser system, and a day later we received an e-mailed surface model in IGES format that duplicated the headform to a high level of accuracy. We imported the model into Pro/Engineer MCAD software, and it came in solid, without requiring any touchup. At $1,500, the cost was indeed less than one-third of what it would have cost had we made the measurements by hand or with a CMM system.
![]() |
It wasn’t cost-effective to do by hand, so engineers hired NVision and got a model they imported to Pro/E for the basis of a design. They saved time, got an accurate model, and they realized a 70 percent cost savings in reverse engineering. |
We got a head start on the project by using the accurate model of the headform provided by NVision as the basis for the design of the goggles. It saved time and ensured accuracy of the design for our client. Aside from a 70 percent cost savings in reverse engineering, and although it’s impossible to estimate how much, it also saved money during the rest of the design process when geometries are checked and finalized. The design easily passed the safety tests and is currently in the early stages of production. We have since used NVision to scan a field hockey stick that will be used as the basis for a newer design.
Kevin Vititoe is a senior industrial designer at Priority Designs. He earned an industrial design degree at Ohio State University. You can contact him about this article via e-mail sent to [email protected].
Subscribe to our FREE magazine,
FREE email newsletters or both!Latest News
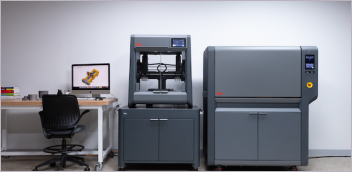
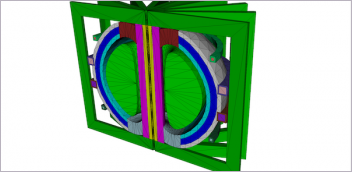
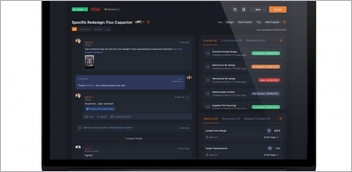
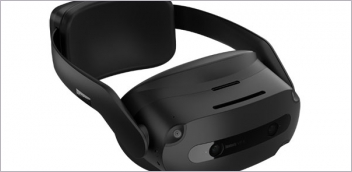