Save Money & Maximize Performance with ANSYS Mechanical 16.0 on Intel Platforms
Latest News
March 2, 2015
Dear Desktop Engineering Reader:
These are interesting times in engineering analysis, and multi-core workstations and HPC (high-performance computing) are a huge part of it. Things like higher memory bandwidth, larger cache sizes, solid-state drives, faster interconnects and so on have shorten simulation times. Ironically, CPU clock rates, while faster, are not increasing at a rate anywhere near as briskly as they did 10, 15 or 20 years ago. This is where the shift to parallel computing has provided substantial performance improvements, giving you a faster time to solution. It exploits available multiple CPU cores to increase the number of computations that can run at each clock cycle.
But engineers inject their own bit of irony into this scenario. Simply put, you abhor a vacuum. As time to solution became faster, you people started making your models more complex to take advantage of both your new computational power and the time saved compared to your previous processes. You increased mesh density, investigated gnarlier non-linear behaviors or maybe “just” used the time you gained to run more iterations of your simulation. Whatever your wont may be, your need for speed caused software and hardware developers to work more closely with each other to deliver you more of what you need. And working closely together is exactly what ANSYS and Intel have done with the recently released version 16.0 of the ANSYS line of products.
Now, the ANSYS Structural Mechanics software suite – ANSYS Mechanical and ANSYS Structural, for example – has supported parallel processing for more than 20 years. When the company recently released the 16.0 version of the suite, the software contained a number of capabilities that let you exploit Intel’s newest generation of multi-core processor and coprocessor technologies. That means even more ANSYS physics algorithms are parallelized to better use the hardware.
But it also means that Intel and ANSYS worked together to test, optimize and deliver code that provides you both robustness and efficiency. In particular, ANSYS Mechanical 16.0 is said to take full advantage of Intel E5 v3 series Xeon processors and Intel Xeon Phi coprocessors. The combination should bring new levels of simulation performance to your HPC environment.
So what’s really in it for you? Well, that’s going to be the subject of an upcoming webinar called “Save Money & Maximize Performance with ANSYS Mechanical 16.0 on Intel Platforms” to be broadcast live on March 17 and again on March 19. Both the Windows and Linux versions of ANSYS Mechanical 16.0 can now leverage one or more Intel Xeon Phi coprocessors, which, according to ANSYS, can provide you with “spectacular sparse solver performance.”
The webinar will also explain how users of ANSYS Mechanical 16.0 can benefit from the latest generation of Intel Xeon E5 v3 processors and Xeon Phi coprocessors and how you can upgrade qualifying systems to these processors and coprocessors cost-effectively.
Some of the performance gain figures I’ve seen on the synergy between ANSYS Mechanical 16.0 and Intel E5 v3 series Xeon processors and Intel Xeon Phi coprocessors the merit the description “game changer.” You should not miss this webinar. It’s only an hour, but implementing what you will see can save you days or weeks of simulation time. You can register for the “Save Money & Maximize Performance with ANSYS Mechanical 16.0 on Intel Platforms” webinar at the date that works best for you at the other end of today’s Check it Out link.
Thanks, Pal. – Lockwood
Anthony J. Lockwood
Editor at Large, Desktop Engineering
Subscribe to our FREE magazine,
FREE email newsletters or both!Latest News
About the Author

Anthony J. Lockwood is Digital Engineering’s founding editor. He is now retired. Contact him via [email protected].
Follow DE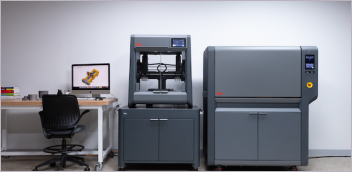
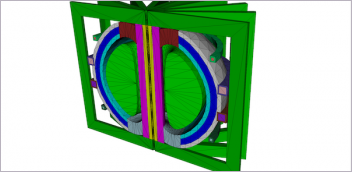
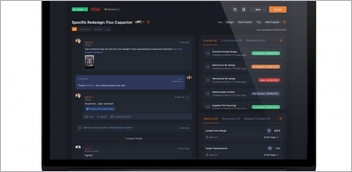
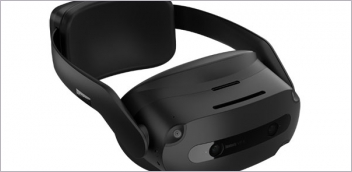