
Latest News
May 9, 2017
The latest release of Siemens’ Solid Edge software (Solid Edge ST10) features new design technology for working with scanned data and topology optimizations, enhanced fluid flow and heat transfer analysis, and cloud-based collaboration tools, as well as improved technical documentation tools.

Solid Edge ST10’s newly integrated generative topology optimization, combined with Siemens’ Convergent Modeling technology, enables designers to improve product design efficiency by streamlining the ability to work with imported geometry, according to the company.
“Generative can produce great designs, but what if I need to change it?” asked Dan Staples, VP, Mainstream Engineering at Siemens PLM Software, during a presentation of ST10 to the press at the Siemens PLM Connection Americas conference May 8-11. “3D scanning from points to CAD is the easy part, then you spend days surfacing it. Additive manufacturing is awesome, but you need to design to take advantage of it.”
One challenge to the modern design workflow is working with faceted designs and solid models. Convergent Modeling is intended to simplify work with geometry consisting of a combination of surfaces, facets and solids—such as those created by importing third-party files, 3D scanning or through topology optimization.
“We import many 3D models for components like lamps and cushions in a faceted format,” said Ricardo Espinosa, via a press release. Espinosa is R&D Engineering Manager at furniture designer and manufacturer, Kimball International, who beta tested ST10. “The new Convergent Modeling technology that underlies Solid Edge ST10 will enable us to work faster and more flexibly with this data.” (Editor’s note: We reported on Kimball’s use of Solid Edge in “Old School Design Meets New Reverse Engineering Technology.”
For an overview of Siemens’ Convergent Modeling functionality, which is in NX and Solid Edge, watch this video from Siemens PLM Software:
New topology optimization technology and new simulation capabilities in Solid Edge ST10, such as integrated fluid flow analysis, eliminate the need to transfer data between different applications. Topology and fluid flow and heat transfer analysis can be done directly in Solid Edge. The simulation technology is a result of Siemens PLM Software working with Mentor Graphics, which it acquired this year.
“Now that Mentor is part of Siemens, you’ll see more and more of us working together,” said Staples at the Siemens PLM Connection conference May 8. “You’ll see further simulation technology integrations in Fall 2017.”

Enhancements to ST10’s integrated computer-aided manufacturing (CAM) enables efficient programming of CNC machine tools, and the ability to define complex sheet metal components, optimized for manufacturing. New additive manufacturing tools enable users to 3D print parts in house or access a network of additive manufacturing services.
Solid Edge ST10 also includes enriched publication features to create detailed illustrations of designs. These documents are associative to the original design information, enabling rapid updates to the documentation when the design changes. New enhancements to built-in Solid Edge data management and improved integration with Siemens’ Teamcenter software delivers scalable product data management, according to Siemens PLM Software. Component classification and off-line working are now supported for Solid Edge using the embedded Teamcenter integration.
The Solid Edge portal will offer a cloud-based solution to collaborate with other users, suppliers and customers, helping to simplify communication in product development cycles. Offering a new way to work cooperatively, the portal allows users to upload and manage files in cloud-based folders, with multi-platform browser-based viewing of Solid Edge and many other CAD applications.
“Digitalization is leveling the playing field, providing unlimited opportunities for small-to medium-sized businesses to disrupt industry,” said John Miller, senior VP and GM at Siemens PLM Software, via a press release. “The release of Solid Edge ST10 provides a portfolio of next generation product development tools that will enable our manufacturing customers to fully collaborate in the digital economy.”
Solid Edge ST10 is scheduled to ship in summer 2017.
For more information visit Siemens PLM Software’s Solid Edge ST10 page.
Sources: Press materials received from the company, information from the company’s website and presentations at the Siemens PLM Connection conference.
Subscribe to our FREE magazine,
FREE email newsletters or both!Latest News
About the Author

Jamie Gooch is the former editorial director of Digital Engineering.
Follow DE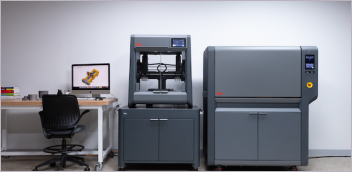
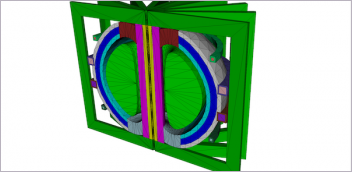
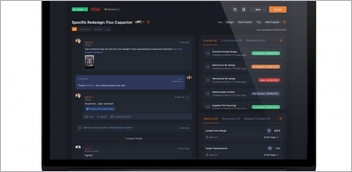
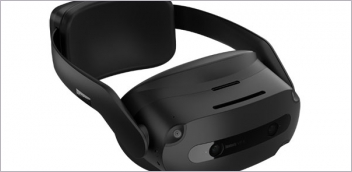