Simulate Mechanical Drive Systems
Latest release of Adams/Machinery from MSC Software expands machinery modeling and simulation capabilities.
Latest News
October 30, 2013
![]() Adams/Machinery version 2013.2. Image courtesy of MSC Software Corp. |
MSC Software Corp. (Santa Ana, CA) has announced the 2013.2 version of Adams/Machinery, its analysis and simulation software suite for mechanical drive systems. Adams/Machinery version 2013.2 is said to provide improved ease of use, an enhanced collection of machine component libraries, and performance improvements that “significantly reduce” modeling times.
MSC Software describes Adams/Machinery as enabling engineers working in aerospace, automotive, heavy industry, industrial machinery, and similar equipment industries to build, evaluate, and manage the complex interactions relating to motion, structures, actuation, and controls for product design optimization including performance, safety, and comfort. The company adds that with Adams/Machinery users can build functional virtual prototypes from common machinery components ranging from gears to bearings to motors as well as predict system dynamic responses.
Adams/Machinery is said to provide modeling automation specific to machinery component types, which can provide early insight into design performance. It deploys with a wizard-driven modeling environment from which users create machinery models even before CAD information is available. As well, it can use CAD data to predict mechanical problems that can lead to product failure and high warranty costs.
![]() Adams/Machinery version 2013.2. Image courtesy of MSC Software Corp. |
Adams/Machinery is fully incorporated inside the Adams/View user interface environment. Engineers can use Adams/View to build models of mechanical systems and simulate full-motion behavior as well as analyze multiple design variations. However, Adams/Machinery’s multiple modeling productivity modules enable them to create common machinery components “much more rapidly than with generic standard Adams/View model construction functionality alone,” according to the company.
Version 2013.2’s collection of machine component libraries has been expanded with a new electric motor module that the company says represents electric motors with more sophistication than simple kinematic motions or potentially complicated self-authored torque functions or subroutines. With the electric motor module, engineers can calculate necessary motor sizing, predict the impact of motor torque on a system, and obtain a “realistic” drive signal for the rest of the machine components, according to the company. Engineers can use an external method created by MSC Software’s Easy5 controls and systems simulation software or the Simulink block diagram environment from the MathWorks to define motor torque, and they can use different modeling methods for different applications.
![]() Adams/Machinery version 2013.2. Image courtesy of MSC Software Corp. |
Among the additional enhancements now available in the individual Adams/Machinery 2013.2 machine component modules are:
- Bearing – Predict bearing loads, study the effect of changing bearing parameters, and predict bearing service life.
- Belt – Predict load history, analyze belt slippage, study the effect of belt compliance, and avoid power transmission failure. A new 3D belt method for non-planar pulley-belt simulation is now available.
- Cable – Calculate cable tension, assess load history on pulleys, analyze potential for cable slippage, and predict winching effects.
- Chain – Analyze vibration due to preloads, predict load history of sprockets, and avoid tensile failure. A new 3D chain method for non-planar sprocket-chain simulation is now available, and a new discretized 3D method supports roller chains.
- Gear – Study the effect of backlash, predict contact force between gear pairs, study gear friction, and mitigate gear rattle. In addition to the current spur, helical, and bevel gears, Adams/Machinery 2013.2 extends support to three new gear types: worm, rack and pinion, and hypoid gears.
To learn more about Adams/Machinery 2013.2, license options (token and standalone availability), and other requirements, go to MSC Software.
Watch an on-demand webinar about Adams/Machinery.
Download the Adams/Machinery brochure.
Download the Adams/Machinery data sheet.
Access a series of brief animations on the modules and features available in Adams/Machinery.
See why DE’s Editors selected Adams/Machinery Version 2013.2 as their Pick of the Week.
Sources: Press materials received from the company and additional information gleaned from the company’s website.
Subscribe to our FREE magazine,
FREE email newsletters or both!Latest News
About the Author

Anthony J. Lockwood is Digital Engineering’s founding editor. He is now retired. Contact him via [email protected].
Follow DE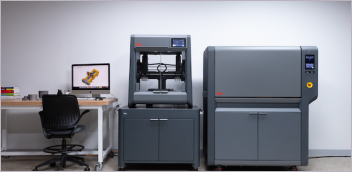
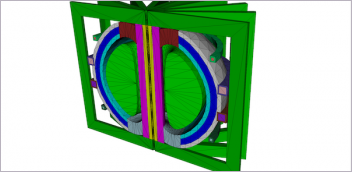
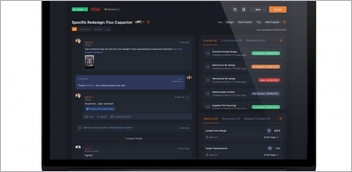
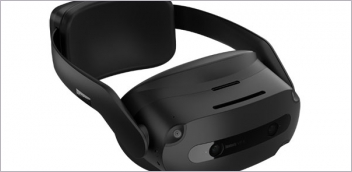