Sizing Up the Modeling World
Latest News
March 3, 2008
By Jim Cooper, Maplesoft
What if you had a part designed in a 3D modeling system and wanted to find out quickly how good this part would be for different material and loading conditions? Do you launch your favorite FEA solver and then mesh, solve, and try to interpret reams of data? Do you sketch free-body diagrams on an envelope and try to do a basic reaction force calculation? What if this part typically gets a good knock during operation and you need to figure out how to minimize the vibration? Which software do you turn to?
This little scenario highlights a major problem within engineering modeling: the divide that separates the 3D and FEA modeling world from what many call the “1D” modeling world. More technically, “lumped parameter” representation: various physical details of the system components collapsed or lumped into singular points.
The main interest in 1D modeling is general system behavior. For example, when modeling a mechanical device, you would ignore the actual machined shape. The advantage of 1D modeling is that you can very quickly determine the most important system dynamics, including those needed for control applications. This is the domain of the current Maplesoft products that provide tools to quickly develop system models.
The problem is, of course, that everything has a 3D shape. The more realistic 3D representations are, of course, the domain of the CAD or solid modeling systems and FEA. Typically, 3D modeling helps to determine manufacturability or shape-dependent analysis for strain or performance in fluid environments. When it comes to figuring out whether all of the parts, when put together, move as expected, most 3D systems run out of steam because of the overhead they carry to support all of the geometric detail.
Recently, Maplesoft and several leading CAD companies have begun taking the first steps in bringing these worlds together. Through this collaboration, users will soon be able to combine full geometric solid models with the wide range of calculation and visualization tools for system level analysis in an easy, convenient, and systematic way. You can design a part in your CAD system, transfer parameters to Maple using the extensive mathematical library, quickly perform your model calculations, and then automatically adjust your CAD model based on results. No mesh, no fuss.
In many ways, this first step is simply the result of connecting the “plumbing” between the systems. Our design teams are already progressing toward the next phase, where fully detailed 3D models will seamlessly integrate with the graphical component modeling environments that are highly effective within the 1D dynamic modeling world. If things go according to plan, the switch between the system view for overall behavior to component view for individual parts will be completely seamless. In many ways, this constitutes a fundamentally new and integrated approach to engineering modeling.
The lesson here, I believe, is to never be satisfied with a particular set of tools regardless of how popular or established the tool may be. The emerging engineering challenges, whether they are greener vehicles or missions to Mars, are forcing engineers and scientists of all stripes to work effectively and creatively with each other. Shouldn’t our software tools do the same?
Jim Cooper is president and CEO of Maplesoft. You can send e-mail about this commentary to [email protected].
Subscribe to our FREE magazine,
FREE email newsletters or both!Latest News
About the Author

DE’s editors contribute news and new product announcements to Digital Engineering.
Press releases may be sent to them via [email protected].
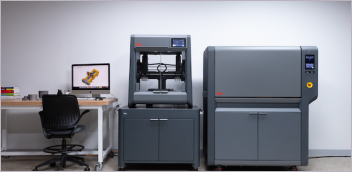
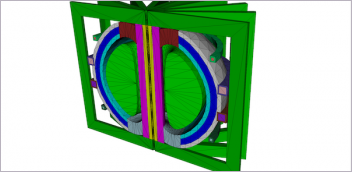
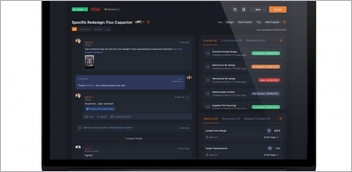
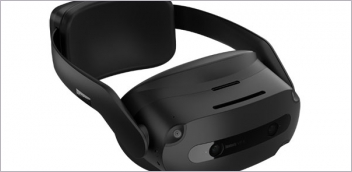