Stratasys to Offer SABIC’s ULTEM 9085 High Performance Thermoplastic for FDM Additive Fabrication
High-performance thermoplastic is widely used in aerospace and should attract other industries.
Latest News
December 3, 2008
By DE Editors
Stratasys (Minneapolis, MN) made the announcement that it will offer SABIC’s ULTEM 9085, a high-performance thermoplastic for direct digital manufacturing and rapid prototyping. Available in the first quarter of 2009, the material is intended for the FDM additive fabrication process.
The ULTEM 9085 is characterized as a strong, lightweight, flame-retardant thermoplastic widely used in aircraft interiors. Among its features is its V-Ø rating for flame, smoke and toxicity (FST). The fact that ULTEM 9085 is made available for the FDM additive fabrication process makes it possible to do direct digital manufacturing and rapid prototyping with this material for the first time.
ULTEM 9085 will be available for the Stratasys additive fabrication machines ‑ the FDM 900mc and FDM 400mc. Prior to this announcement, ULTEM 9085 was only available for conventional manufacturing methods. Originally developed to help the aerospace industry boost fuel efficiency and safety, the material is strong and flexible while at the same time produces interior parts that are 5 to 15 percent lighter than other aerospace plastics. The fact that the ULTEM 9085 is certified for use on commercial aircrafts, means that manufacturers can bypass a lengthy certification process.
ULTEM 9085 is heat-resistant up to 320° F (160° C) and is inherently flame-retardant, offering full FST compliance including OSU heat release of less than 55/55, or 55 kw min/m2 for heat release and 55 kw/m2 for peak heat release.
Stratasys expects that other industries besides aerospace will benefit from the availability of ULTEM 9085 for FDM prototyping and production, such as marine and automotive. The company announced ULTEM 9085 at the EuroMold Show in Frankfurt.
For further information, visit Stratasys.
Sources: Press materials received from the company and additional information gleaned from the company’s website.
Subscribe to our FREE magazine,
FREE email newsletters or both!Latest News
About the Author

DE’s editors contribute news and new product announcements to Digital Engineering.
Press releases may be sent to them via [email protected].
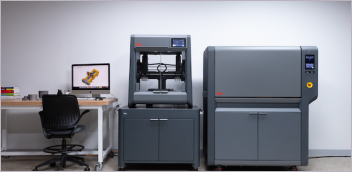
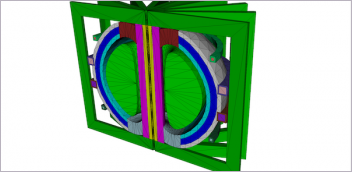
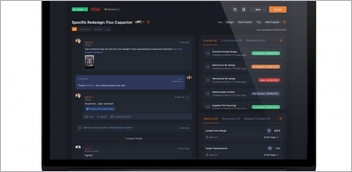
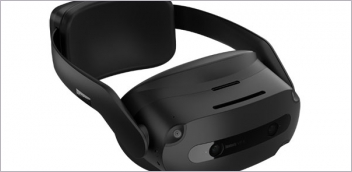