The Impact of Globalization on Design
Latest News
May 1, 2008
By Adina Shorr, Objet Geometries
![]() |
Until now, the “global” aspect of manufacturing has primarily been focused on actual mass production in factories located in developing countries. Given this reality, many North American and Western European companies follow a marketing strategy of informing consumers that their product lines have been designed locally, at home, while actually being manufactured somewhere else. For example, the label on a recently purchased iPod reads, “Designed in California. Made in China.” Yet just as market pressures have led to the globalization of the shop floor, these same common denominators are dictating similar globalization of the design studio as well.
Global cooperation — essentially off-shoring — at the design stage of the product development cycle can yield many economic and practical benefits, and effectively address real business needs. The sharing of design and other related critical information allows businesses to better cope with ever-escalating, concurrent demands for quality, customization, and aesthetic innovation.
As an example, once headquarters has initiated a basic product design, that design can be further developed, refined, and validated by local engineers at close proximity to the manufacturing plant. In this fashion, product design becomes more efficient, because it is an increasingly collaborative effort, leveraging better use of all resources in the development and design chain. In a nutshell, this type of global sharing of product design processes is the next-step response to the basic market paradigm of “better-faster-cheaper.”
In order for this scenario to develop further, however, designers must learn to communicate in a universal language, a language instantly understood by their design partners — the language of 3D modeling. This common language levels the field for all partners, bridging linguistic and cultural differences, as well as distance, clearly communicating design intent and function.
One of the clearest ways to aid in that communication is to put a physical model of the proposed part into a design partner’s hands. Printing a rapid prototype model using design data fuels creativity, allowing a greater degree of design testing and product validation. It also helps relate increasingly complex design concepts while cutting down on error, and facilitates an accelerated move from 2D to 3D design techniques. It is this working methodology that will propel the design-to-market process.
Without a doubt, the mechanical CAD evolution is fueling and driving the 3D-printing revolution. In 2006, there were more than two million commercial MCAD seats in use, yet output systems capable of transforming designs into physical models amounted to only one percent! In addition to using 3D printers for design verification, 3D printing technology will also be able to “fax” designs to partners located anywhere in the world. When combined with the need to communicate and deliver complex designs with simplicity and accuracy, advanced 3D printing technology and its decreasing costs will catapult rapid prototyping into mainstream design, and will make product design a truly global activity.
Adina Shorr is CEO and president of Objet Geometries Ltd. You can send e-mail about this commentary to [email protected].
Subscribe to our FREE magazine,
FREE email newsletters or both!Latest News
About the Author

DE’s editors contribute news and new product announcements to Digital Engineering.
Press releases may be sent to them via [email protected].
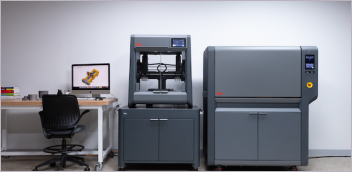
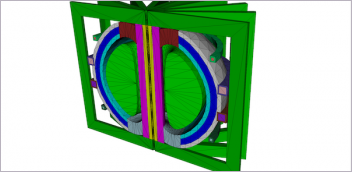
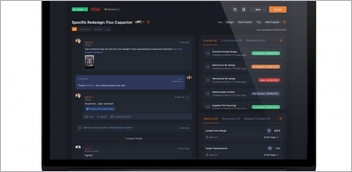
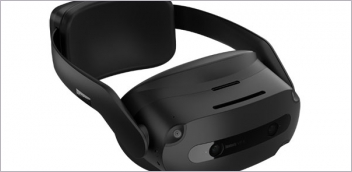