Why 3D-Printed Molds Aren’t Everything They’re Cracked Up to Be
Latest News
March 15, 2016
Dear Desktop Engineering Reader:
Predictions often don’t work out as foretold. If you listened to knuckleheads like me in the early 2000s, you learned that 3D printing plastic or metal molds would’ve pushed out machining metal molds by now. Not quite, according to a blue-chip blog post at the far side of today’s Check it Out link.
What really recommends the post “Why 3D-Printed Molds Aren’t Everything They’re Cracked Up to Be” on the Digital Thread blog is that it’s from Proto Labs. The company is a big provider of fabrication services for 3D plastics and metal printing, milling and turning as well as plastic injection molding.So, it has zero interest in praising rapid metal mold making by trashing 3D printing. Indeed, the post ends by explaining where 3D-printed injection molds can be viable. Still, Proto Labs has every interest in explaining why machined metal molds are often your best bet.
Apparently the inspiration for this post is that clients often ask Proto Labs why it machines most of its injection molds from aluminum or steel rather than 3D print them. Kip Hanson, the blogger, responds by ticking off a number of reasons, ranging from quality to size and from heat resilience to design concerns and comparable costs. He does a nice job of explaining each.
Quality, for example, means secondary operations that can negate some of 3D printing’s perceived advantages. Take the stair-step effect on angled surfaces you get with 3D prints. You have to sand or machine that down. And when it comes to size, EDM equipment can produce part volumes many times greater than a 3D printer.
The discussion on comparative costs of machined molds and 3D prints, a perceived disadvantage of metal molds, is food for thought. Hanson raises a bunch of good points, but the most Homer Simpson “D’oh!” head-slap-worthy moment is that a metal injection mold generally can handle upwards of 10,000 shots of molten plastic while a 3D plastic mold can do maybe 100. Metal 3D printing can be too slow and expensive, albeit ideal for impossible to machine inserts.

The short shot is that “Why 3D-Printed Molds Aren’t Everything They’re Cracked Up to Be” says that 3D printing is great for many jobs but it’s not for mold making. Evenhanded and engaging, this post is one you’ll enjoy while learning a few things. Hit today’s Check it Out link and take a few minutes to give it a read.
Thanks, Pal. – Lockwood
Anthony J. Lockwood
Editor at Large, Desktop Engineering
Read “Why 3D-Printed Molds Aren’t Everything They’re Cracked Up to Be” here.
Subscribe to our FREE magazine,
FREE email newsletters or both!Latest News
About the Author

Anthony J. Lockwood is Digital Engineering’s founding editor. He is now retired. Contact him via [email protected].
Follow DE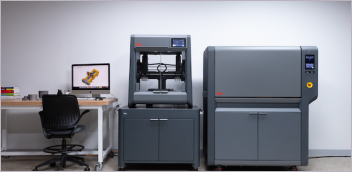
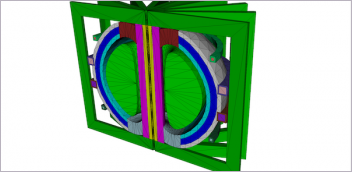
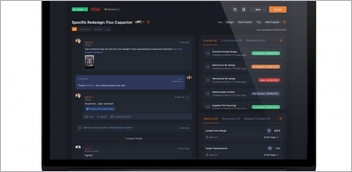
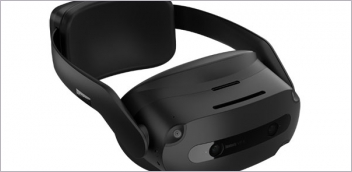