
Simulink model of an experimental setup, and plots comparing pressure in the numerical model and the physical system. Image courtesy of MathWorks.
Latest News
August 6, 2015
Medical technology and modern medicine is constantly seeing new advances. From heart monitors to insulin pumps, new capabilities are being added to these devices, but this also results in increased complexity. To address the challenge of product complexity, MathWorks is helping medical device companies see Model-Based Design (MBD) as an option to help optimize, automate and document the workflow.
MBD implements a hierarchical system model in the center of product development. This means that the executable model serves as a reference throughout design, implementation and testing. With this design method, the workflow is structured to include continuous testing and verification, self-documentation and provides more time for design, says Arvind Ananthan, medical devices industry manager at MathWorks. It also provides the ability to connect the workflow between research, design and implementation— instead of having them siloed.

While MBD is something that companies in the aerospace and automotive industries have been using for decades, it’s now making its way into the medical device design market. This is in part due to the increasingly complex software and greater code requirements. By using multi-domain system modeling, engineers can find ways to catch errors and possible bugs earlier in the design process and fix them while they are cheap to correct.
So what’s one of the ways to implement MBD? While it is a design mindset, it’s also helpful to use MATLAB and Simulink from MathWorks. The platforms are designed to help support this workflow and offer tools such as libraries, automatic reporting and more. “When you combine MathWorks tools, they make a really powerful design environment,” says Carlos Osorio, product applications engineer at MathWorks. “The power of these tools really start coming to life when you start learning how to combine all [the available] toolboxes.”
Osorio recently showcased the capabilities of MBD during a presentation last month at MathWorks using the combined text and visual environment of MATLAB and Simulink. His talk, titled “Designing a Robot Arm using Model-Based Design,” was primarily focused illustrating how the tools and MBD could help solve a complex engineering problem. The challenge? Creating a programmable robot arm with several motors and several mechanical properties.
What these tools provide, Osorio noted, is a more automated workflow. Instead of taking several hours (or days) to calculate a single property of his robot arm by hand, Osorio managed to simulate several design iterations within minutes. “Once you start thinking of a system, going into a graphical environment allows me to look at the system as interconnected pieces the way they are in the actual physical [product],” he says. Such additional features as CAD part import and user-specific libraries also help Osorio bring together a series of text files into a fully working simulation.

While it’s not a medical device, Osorio’s robot arm still illustrated how designs can become quickly complicated — even when they are broken down into separate calculations. But by using MATLAB and Simulink, he was able to expedite the entire design process and efficiently predict how his robot would react to certain parameter choices and input stimuli.
The level of automation and reporting MATLAB and Simulink provide is something that more medical device companies are starting to leverage in their own processes to reduce the amount of time they spend in documenting their work. “What we have been seeing lately is that some of the top engineers who have moved to medical device companies after working in the aerospace and automotive sector for many years, notice the lack of simulation and modeling methodologies, and call us to equip their new employers with our design tools” says Ananthan.
The medical device industry is still trying to catch up to aerospace and automotive, which have leveraged modeling and simulation to properly vet designs before they hit the track or runway, says Ananthan. This lag is due to the large amount of compliance and verification needed for medical device design, but Ananthan observes that part of this growing adoption of MBD can be attributed to startups and a host of industry partners.
“MBD is showing its value in the medical device design space. With MBD, engineers can automatically generate code for embedded deployment and create test benches for system verification, saving time and avoiding the introduction of manually coded errors that have a higher likelihood of occurring with the traditional approach. Errors and bugs can more likely be detected in the simulation stage where it’s a lot cheaper to fix, while minimizing the risk of any potential future recalls,” says Ananthan.
Ananthan notes that while MBD is being used for medical device design, it’ll be a few years before it becomes a widespread practice. But there are companies such as Philips who uses Model-Based Design to develop a digital RF power subsystem for use in MRI systems (for the full story, visit here).
Subscribe to our FREE magazine,
FREE email newsletters or both!Latest News
About the Author

Jess Lulka is a former associate editor for Digital Engineering. Contact her via [email protected].
Follow DERelated Topics
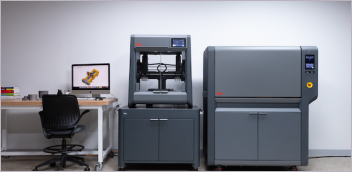
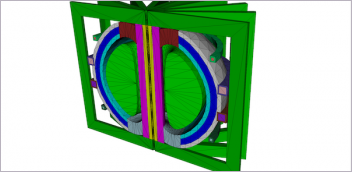
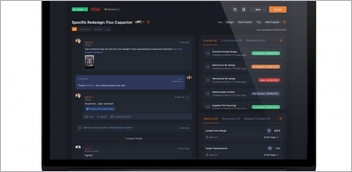
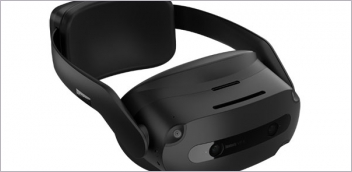