
Latest News
February 3, 2016
Last week some of the top automotive computer-aided engineering (CAE) experts gathered in Troy, MI, to share challenges and best practices when simulating lightweight materials at the Lightweight Materials Modeling, Simulation and Crash Safety Congress, which focused on composite modeling and multi-material joining simulation.
“We’re solving some of the problems — there’s a lot of problems we haven’t even started on, especially ... composites,” said Conference Chair Eric DeHoff, principal engineer, Safety CAE, at Honda R&D as he kicked off the first day with a call for participation from the audience.
It’s a safe bet that all automakers are working hard to incorporate more lightweight steels, aluminum, magnesium and composite materials into their vehicles. They all face the same challenge: improving fuel economy to meet regulations and consumer demand. The most efficient way to do that is to reduce vehicle weight.
Umesh Gandhi, Toyota Research Institute, presents strat. for mod & sim of lightweight materials. #crashsafety pic.twitter.com/VhJs1h0gCB
— Desktop Engineering (@DEeditor) January 26, 2016
“Typically for the IC (internal combustion) engine ... a 6-8% improvement in fuel economy is achieved with a 10% decrease in weight,” said Dr. Umesh Gandhi, principal scientist, Toyota Research Institute, in his day-one keynote. “For electric cars, reducing weight is even more important because range almost doubles by reducing the weight.”
But there are many challenges involved in using lightweight materials, especially safety concerns, the cost for sourcing and manufacturing the materials, as well as predicting design performance. The main issues with the design process are, according to Ghandi, understanding material properties and joining with CAE tools.
Bigger Models, Smaller Structures
Gandhi provided some historical perspective on improving fuel economy while increasing safety. In the ‘80s, finite element models for crash were first widely used. “They used explicit methods and typically the size of the models were 6,000 (elements) with very limited post-processing capabilities,” he said. “The ‘90s are when you see finite element models that are similar to what we see today,” except for the exponential growth of the number of elements as affordable computing power has grown.
“We’re able to have larger models, better geometry, faster computing and better algorithms — but what’s happening now is that the technology is kind of maturing,” Gandhi said. “By increasing further or making larger models, we’re not going to see significant improvements in accuracy. The key challenge that we face today, particularly when trying to use lightweight materials, is material models and the ability to accurately include them in CAE models, and joining.”
To meet that challenge, multiscale modeling is needed to include the microstructure of materials in the design process. Material properties depend on the microstructure, which — especially with composite materials — depends on the material manufacturing process, Gandhi said. “Process defines the final output,” he noted. Unfortunately, material properties are not often available or measurable, so it takes a lot of time and effort to model materials, he said “and you need to plan for that.”
Looking Toward Lattice
Lightweight materials will only take you so far when reducing weight. If you want to go beyond the weight reduction benefits of materials, then you have to consider removing material via lattice structures. Think of a solid part being replaced by an internal web-like lattice to form the structure. That would greatly reduce the weight of the part, but it would also require many design and simulation complications.
“How we design the lattice structure is a big challenge because the tools are not ready,” Gandhi said. “If you think of the lattice shape, there’s no simple way to do it. What is the best lattice design? What type of finite element model should be used?” Then, of course, how will those lattice structures be manufactured?
3D printing is one technology that could be enlisted to solve the manufacturing question, but Gandhi says widespread use of lattice structures in the automotive industry are a lightweighting tool for the future, “maybe 10 years from now.” (See DE’s previous coverage of lattice structures and 3D printing here, and here, and listen to our complimentary webcast on the topic here.)
Subsequent speakers focused on individual research they were conducting to incorporate multiscale modeling into their validation efforts. They including experts from Honda, Ford, GM, academia and the conference sponsors: Owens Corning, Continental Structural Plastics and Engenuity. Of course, lightweighting isn’t just for big automakers and CAE experts. At the conference, Ford’s Dr. Horst Lanzerath, team/technical leader, Advanced Material CAE, made it clear that it would be relying more on its suppliers to provide material data for the parts they provide. Ford is known for its innovation in using lightweight materials to redesign the 2015 F-150 (see DE’s previous coverage: Ford Invests Heavily in Lightweighting Efforts). And, during a conference roundtable discussion, it was mentioned that most design engineers don’t yet understand how to design with new materials.
Corvette panels on display at the Lightweight Materials Modeling, Simulation & Crash Safety Congress. #crashsafety pic.twitter.com/CjA3t1giLu
— Desktop Engineering (@DEeditor) January 26, 2016
To learn more about designing with lightweight materials and validating CAE simulations, you can purchase a post-event video package that includes many of the Lightweight Materials Modeling, Simulation and Crash Safety Congress presentations, or register to attend their 5th Annual Global Automotive Lightweight Materials Detroit 2016 event in August. You can also watch the complimentary, on-demand presentation from DE: “Shed Excess Weight from Products,” for an interactive discussion of the topic with industry experts.
Subscribe to our FREE magazine,
FREE email newsletters or both!Latest News
About the Author

Jamie Gooch is the former editorial director of Digital Engineering.
Follow DE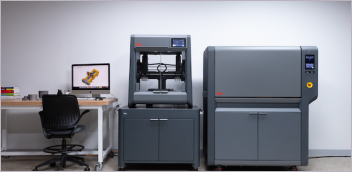
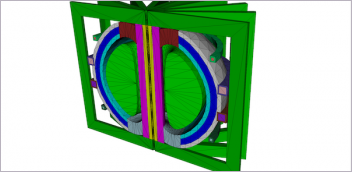
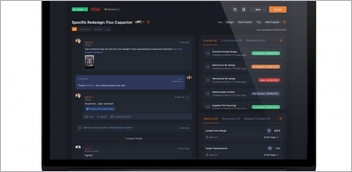
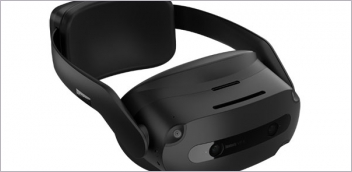