Arena Looks Toward Quality Management

Arena Quality directly connects quality processes to the product record in Arena PLM, creating a closed loop quality system. Image Courtesy of Arena Solutions
Latest News
July 22, 2014
Customers ask and they shall get. It’s the guiding principle for how many design software companies chart a product roadmap, and in the case of Arena Solutions, customers’ repeated requests have spawned Arena Quality, a full-blown quality management module recently added to round out the firm’s cloud-based PLM suite.
As a closed-loop quality solution, Arena Quality direct connects quality processes to the product record in Arena PLM, providing the visibility that will allow engineering and manufacturing teams to rapidly identify, capture, collaborate, and resolve product quality problems. While Arena provided some capabilities for tracking quality issues against items and engineering change orders (ECOs) in prior releases, this is the first complete set of functionality designed for an entire team to manage and lead a continuous improvement effort.
“We saw an opportunity and our customers were asking for it,” says Steve Chalgren, Arena Solutions’ vice president of product management and strategy. “They really want to do continuous improvement and create a really strong quality culture within their environments.”
Quality capabilities, particularly those to support corrective action and preventive action (CAPA), have become a staple of most PLM platforms over recent years as manufacturers have begun to prioritize the discipline to stay steps ahead of the competition. Despite the emphasis on quality and continuous improvement, Chalgren says manufacturers still have fairly immature and disorganized quality processes, most performed manually using paper-based systems and spreadsheets.
While there are standalone quality management solutions, they are typically isolated from the product record, which can create conflict and spark miscommunication between the quality and other product teams, he explained.
That’s where Arena Quality comes in. The capabilities are embedded in the product record, giving stakeholders from engineering, operations, and the supply chain complete visibility into quality issues. Arena Quality also captures all quality processes in an easily navigated history, which can serve as a audit trail for various regulatory compliance efforts, whether for the Food and Drug Administration (FDA), which is critical to medical devices companies, or the International Organization for Standardization (ISO) governing mainstream manufacturers.
Because quality processes vary across manufacturing sites, Arena Quality offers templates, which can be customized to reflect the various phases, attributes, and terminology used by internal quality teams. In addition, the templates help companies get up and running on a quality process in short order, without having to start mapping processes from scratch.
Teams can assign responsibilities at multiple levels, manage schedules, and track progress to final resolution, and emailed notifications are displayed in the Arena PLM dashboard so everyone is kept up to date on outstanding issues. There is also a 21 CFR Part 11 compliant electronic signature capability, eliminating the need to print and manage hard copies.
The video below provides a look at Arena BOMControl, Arena’s bill of materials management tool, which complements the new Arena Quality Module.
Subscribe to our FREE magazine,
FREE email newsletters or both!Latest News
About the Author

Beth Stackpole is a contributing editor to Digital Engineering. Send e-mail about this article to [email protected].
Follow DERelated Topics
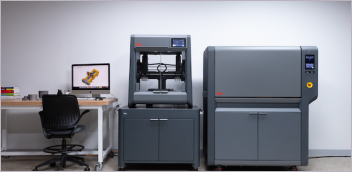
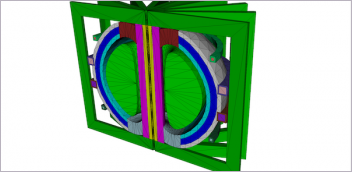
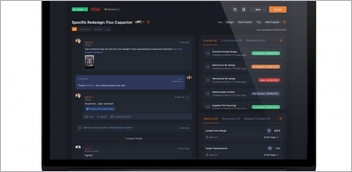
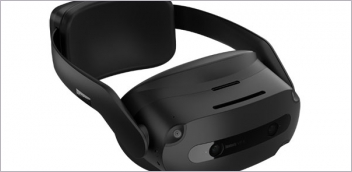