Latest News
October 1, 2010
By Kenneth Wong
As spring arrived last April, international watchmakers and jewelry designers descended on Basel, a border town in Switzerland where Swiss, French and German borders meet. The place is the site for Baselworld, the annual conference where Seiko, Tissot, Raymond Weil and other high-end timepiece merchants come to impress one another and the world.
![]() Early concept sketches of Devon Tread 1. Images courtesy of Jason Wilbur and Devon Works. |
In the crowd of roughly 2,000 exhibitors and 100,000 attendees was Jason Wilbur, a former graphics designer and automotive designer. He was there to show his new creation, dubbed Devon Tread 1.
This newcomer had good reason to be nervous, as he was turning the art of watchmaking inside out—literally. Devon Tread 1 is a radical departure from the typical dial-and-needle timepieces. Its movement hinges on a series of overlapping, interwoven belts, encased in glass. The internal mechanism—the soul of the watch—is in full display, completely visible.
“There’s a formula for creating high-end watches,” says Wilbur. “And I wanted to break that formula.”
To break the rules of timekeeping, Wilbur resorted to what he used to design cars and create brochures: SolidWorks CAD and Bunkspeed HyperShot (recently rebranded as Bunkspeed SHOT).
![]() An exploded view of Devon Tread 1 showing its internal components, rendered in Bunkspeed HyperShot. Image courtesy of Jason Wilbur and Devon Works. |
From Logos and Cars to Timepieces
Wilbur began his studies in upstate New York, with a fine arts course he never finished. It was interrupted when his internship turned into a real job. He drifted into graphics design, and when he grew weary of creating logos and brand collaterals, he enrolled in a transportation design course at the Art Center College of Design in Pasadena, CA. This time, he would complete the program, graduating in 2005.
“I like cars, but my real love is design,” he says. “I’m also an artist, so I never want to do what everyone else is doing. I want to do something new.”
For the next four years, he was employed by Honda to design mass-market vehicles and concept cars. “I’ve always been fascinated by motors and engines,” he says. “There’s a certain beauty in the way they function with mathematical precision.”
Eventually, he decided to flex his creative muscles beyond automotive design. This time, his challenge was to be time itself. When people listen to their watches, they hear ticking. Wilbur hears something else: the heartbeat of a mechanical life form.
“Watches seem to have the same kind of soul ]as cars],” he muses. “Both are mechanical, with central nervous systems and characters.”
Wilbur recognizes that cell phones are far more accurate at keeping time than a watch is. For a watch to be relevant and appealing, he decided, it had to do more than tell time.
“It needs to be emotional sculpture, ]something] driven more by passion than its mechanical function,” he says.
Wilbur’s timepiece has hundreds of components, with very few that are standard off-the-shelf parts. He knew that if he’d provided manufacturers with 2D sketches, he’d be taking a risk that they might not be interpreted as intended—or worse, the finished pieces might not assemble correctly.
“I used SolidWorks because I found it to be the best tool to make mechanical items beautiful, to bring out the subtleties in them,” he says. Though Wilbur sculpted the timepiece aesthetically to his liking, he also knew that he’d have to turn his idea over to engineers to adjust the mechanical components to the appropriate ratio, scale and dimensions. When the time came, exchanging 3D SolidWorks files with engineers helped him create an iterative workflow.
The belts, the most delicate elements in the piece, gave Wilbur pause.
“They needed to be thin,” he recalls. “But they mustn’t bend or flex with exposure to the sun and weather elements.”
He remembered a type of glass-reinforced nylon material used in avionics. “You could have ]that material] at 150ºF heat or 20ºF below zero without worrying about it.”
A Time to Render
Before his watch project was picked up by Devon Works, a Los Angeles-based design lab, Wilbur was looking for funding. He needed to raise roughly half a million dollars, he estimated. He judged—correctly, as it turned out—that photorealistic renderings created from a 3D model would inspire more confidence than 2D sketches could ever do. For this purpose, he turned to Bunkspeed HyperShot, a rendering program meant for those unfamiliar with typical rendering jargons and technicalities.
Devon Tread 1’s time window is made of scratch-resistant, anti-reflective polycarbonate crystal with bulletproof toughness. The watch is manufactured by a California aerospace engineering company.
At Baselworld, Wilbur wore an early model of Tread 1 as he made his way through the exhibit halls. He fully anticipated snickers and skepticism from traditional watchmakers. But instead, “Everybody welcomed me into the world of fine watchmaking,” he recalls.
Ready for its Close-up
Devon Tread 1 appeared on the cover of a recent issue of Watch Journal, a magazine devoted to luxury watches. Normally, the magazine would use photographs of the star watch. Devon Tread 1’s debut in the publication marks the first time the magazine used a rendered image on the cover.
Announcing the availability of limited editions of Devon Tread 1, Devon Works described it as “a big, bold, sexy declaration of independence from the status quo.” In most cases, that would be hyperbole. With Tread 1, however, it’s a fitting description.
Wilbur’s masterpiece goes for an estimated $15,000 (roughly the price of a Honda Civic sedan).
A review of Bunkspeed SHOT is scheduled to appear in the November issue of DE. For a comparison of Bunkspeed SHOT and its closest competitor, Luxion KeyShot 2, read “One Scene, Two Shots,” here.
More Info:
Bunkspeed SHOT
Kenneth Wong writes about technology, its innovative use, and its implications. One of DE’s MCAD/PLM experts, he has written for numerous technology magazines and writes DE’s Virtual Desktop blog at deskeng.com/virtual_desktop/. You can follow him on Twitter at KennethwongSF, or send e-mail to [email protected].
Subscribe to our FREE magazine,
FREE email newsletters or both!Latest News
About the Author

Kenneth Wong is Digital Engineering’s resident blogger and senior editor. Email him at [email protected] or share your thoughts on this article at digitaleng.news/facebook.
Follow DE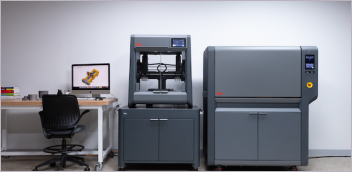
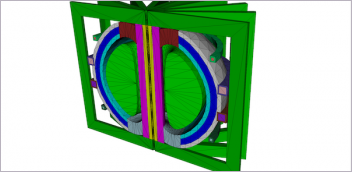
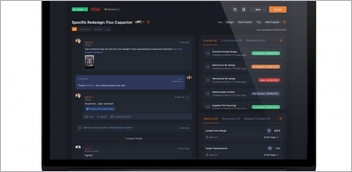
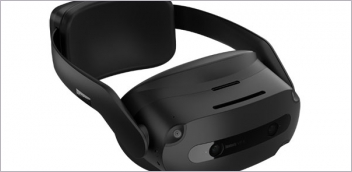